Iron has been known to mankind from early civilization. In fact, a period of history, the “iron age,” is named for the widespread use of this metal. For almost a thousand years, it remained as the single most-used metal, and its use in mechanization made the industrial revolution possible.
Iron, after oxygen, silicon and aluminum, is the fourth most abundant element in the earth’s crust. It is the prime constituent of earth’s core along with nickel. Its abundance in the crust is 5.63%. Its concentration in the seawater is about 0.002mg/L. The principal ores of iron are hematite, Fe2O3; pyrite, Fe2S2; ilmenite, FeTiO3; magnetite, Fe3O4; siderite, Fe2CO3; and limonite [FeO(OH)]. It also is found in a number of minerals, such as corundum, as an impurity. It also is found in meteorites.
Iron occurs in every mammalian cell and is vital for life processes. It is bound to various proteins and found in blood and tissues. The iron-porphyrin or heme proteins include hemoglobin, myoglobin and various heme enzymes, such as cytochromes and peroxidases. Also, it occurs in non heme compounds, such as ferritin, siderophilin, and hemosiderin. Hemoglobin, found in the red blood cells, is responsible for transport of oxygen to the tissue cells and constitutes about two-thirds (mass) of all iron present in the human body. An adult human may contain about 4 to 6 grams of iron.
Iron is the fourth most abundant element in the earth’s crust (5%). It is a transition metal and is placed within the d-block of the periodic table and naturally occurs coordinated with other elements. It is mainly extracted from hematite (Fe2O3) and limonite (Fe2O3·3H2O), although other ores, such as magnetite (Fe3O4), siderite (FeCO3), and taconite (an iron silicate), are also the key sources. Iron is used principally for structural materials, primarily steel, an iron carbon alloy. It is also used in magnets, dyes, pigments, abrasives, and polishing compounds (e.g., jeweler’s rouge).
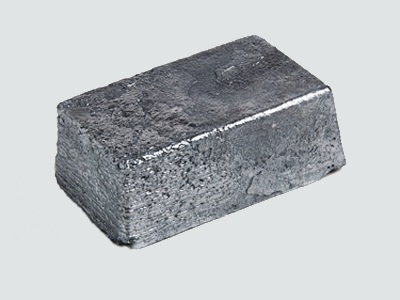
Reduced iron is elemental iron obtained by a chemical process in the form of a grayish black powder, all of which should pass through a 100-mesh sieve. It is lusterless or has not more than a slight luster. When viewed under a microscope having a magnifying power of 100 diameters, it appears as an amorphous powder, free from particles having a crystalline structure. It is stable in dry air.
Accurately weigh approximately 200 mg of the sample and transfer it into a 300 ml Erlenmeyer flask, add 50 ml of a dilute sulfuric acid solution (TS-241). Use a plug containing a Bunsen valve (the production method is to insert a glass tube connected with a short segment of rubber tube to the plug. The side of the rubber tube has a long slit while the other side is inserted of a glass rod so that the gas can escape and the air can’t enter). The solution was heated on a steam bath to dissolve the iron. After cooling, dilute with 50 ml of freshly boiled and cooled water. Add 2 drops of the test solution (TS-162) to 0.1 mol/L
Apply cerium sulfate titration to until the red color becomes light blue color. Each ml of 0.1mol/L of high cerium sulfate are equivalent to 5.585 mg of iron (Fe).
The method is the same as that of "reduced iron (01219)”.
Industrial uses of iron as carbon steels are numerous and surpass any 410 IRONother alloys. Carbon steels are alloys of iron containing carbon in varying proportions, usually up to 1.7% carbon. Other metals also are incorporated into carbon steels to produce low-alloy steels. Such metals are usually nickel and chromium and are classified as stainless steel, tool steels, and heat-resistant steels. Non-steel iron alloys such as cast iron, wrought iron, nickel iron and silicon iron also have many important applications. Another important application of iron is as an industrial catalyst. It is used in catalyst compositions in the Haber process for synthesis of ammonia, and in Fischer-Tropsch process for producing synthetic gasoline.The followings are some examples of common applications:
- pharmaceuticals, pesticides, powder metallurgy and so on;
- as a hot hydrogen generator, gel propellant, combustion activator, catalyst, water cleaning adsorbent, sintered active agent, etc;used for powder metallurgy products, all kinds of mechanical parts and components products, cemented carbide products, etc;
- as a reducing agent as well as being used for iron salt manufacturing and electronics industry;
- as nutritional supplements (iron fortifier),for casting,or as reducing agent;
- in the electronics industry, powder metallurgy.
Most iron produced today is from its oxide minerals, hematite and magnetite. The process involves reducing mineral iron with carbon in a blast furIRON 411nace. There are several types of blast furnaces which vary in design and dimensions. The overall processes, however, are more or less the same. One such process is outlined below:
The mixture of ore, coke and limestone is fed into the blast furnace from the top. The materials are preheated to about 200°C in the top most zone. Hematite is partially reduced to magnetite and then to FeO by the ascending stream of carbon monoxide formed at the bottom and mid zones of the furnace resulting from high temperature oxidation of carbon. The ferrous oxide FeO formed at the top zone is reduced to metallic iron at about 700°C in the mid zone by carbon monoxide. A hot air blast at 900°C passes through the entire furnace for a very short time (usually for a few seconds). This prevents any gassolid reaction product from reaching equilibrium. In the temperature zone 700 to 1,200°C ferrous oxide is completely reduced to iron metal by carbon monoxide. Also, more CO is formed by oxidation of carbon by carbon dioxide. Further down the furnace at higher temperatures, around 1,500°C, iron melts, dripping down into the bottom. Also, in this temperature zone acidic silica particles react with basic calcium oxide produced from the decomposition of limestone, producing calcium silicate. The molten waste calcium silicate also drips down into the bottom. In the hottest zone of the blast furnace, between 1,500 to 2,000°C, some carbon dissolves into the molten iron. Also at these temperatures any remaining silicates and phosphates are reduced to silicon and phosphorus, and dissolve into the molten iron. Additionally, other tract metals such as manganese dissolve into the molten iron. The impure iron melt containing about 3 to 4% carbon is called “pig iron”. At the bottom, the molten waste slag floats over the impure pig iron melt that is heavier than the slag melt and immiscible with it. Pig iron is separated from the slag and purified for making different types of steel.
Chemical reactions and processes occurring in various temperature zones of blast furnace are summarized below:
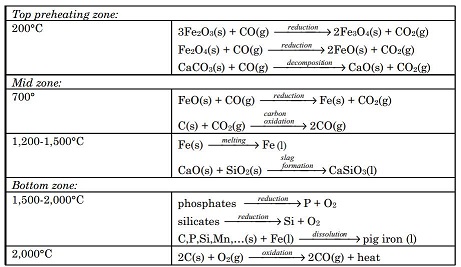
Pig iron produced in the blast furnace is purified and converted to steel in a separate furnace, known as a basic-oxygen furnace. Jets of pure oxygen gas at high pressure are blown over and through the pig iron melt. Metal impurities are converted into oxides. Part of the dissolved carbon in the impure iron melt is converted into carbon dioxide gas. Formation of SiO2, CO2, and other metal oxides are exothermic reactions that raise the temperature to sustain the melt. A lime flux (CaO) also is added into the melt, which converts silica into calcium silicate, CaSiO3, and phosphorus into calcium phosphate, Ca3(PO4)2, forming a molten slag immiscible with molten steel. The lighter molten slag is decanted from the heavier molten steel.
China pyrrhotite-type sulfur pyrite mine has less of mining hills resources. Take the MinXi mine in the DaTian City, Fujian Province and Zhangjiagou mine in Dandong City, Liaoning Province as the representatives; both of them are underground mining mines. The former applies the Housing pile mining method while the later one uses the section mining method. The pit mining process is the same as the method of "phosphate rock." Beneficiation methods include flotation process and flotation-magnetic combined process.
Iron Powder: GRAS (FDA, § 184.1375, 2000); Inhalation of dust can cause pneumoconiosis. Operation personnel should wear overall, wear dust masks and other labor insurance products. Production equipment should be closed, the workshop should be well-ventilated. Be sure to pay attention to dust protection.
Carbonyl iron is elemental iron produced by the decomposition of
iron pentacarbonyl as a dark gray powder. When viewed under a
microscope having a magnifying power of 500 diameters or
greater, it appears as spheres built up with concentric shells. It is
stable in dry air.
Silver-white malleable metal. The only metal that can be tempered. Mechanical properties are altered by impurities, especially carbon.Iron is highly reactive chemically, a strong reducing agent, oxidizes readily in moist air, reacts
with steam when hot, t
Pure iron is a silvery-white, rather soft metal which is both malleable and ductile at room
temperature. Its physical properties, however, are profoundly altered by the presence of
trace amounts of other elements, and since pure iron finds little industrial use, the physical properties of the numerous steels are in many respects more important.
Pure iron is a silvery-white, hard, but malleable and ductile metal that can be worked andforged into many different shapes, such as rods, wires, sheets, ingots, pipes, framing, and soon. Pure iron is reactive and forms many compounds with other elements. It is an excellentreducing agent. It oxidizes (rusts) in water and moist air and is highly reactive with most acids,releasing hydrogen from the acid. One of its main properties is that it can be magnetized andretain a magnetic field.The iron with a valence of 2 is referred to as “ferrous” in compounds (e.g., ferrous chloride= FeCl2). When the valence is 3, it is called “ferric” (e.g., ferric chloride = FeCl3).Iron’s melting point is 1,535°C, its boiling point is 2,750°C, and its density is 7.873g/cm3.
There are 30 isotopes of iron ranging from Fe-45 to Fe-72. The following arethe four stable isotopes with the percentage of their contribution to the element’s naturalexistence on Earth: Fe-54 = 5.845%, Fe-56 = 91.72%, Fe-57 = 2.2%, and Fe-58 =0.28%. It might be noted that Fe-54 is radioactive but is considered stable because ithas such a long half-life (3.1×10+22 years). The other isotopes are radioactive and areproduced artificially. Their half-lives range from 150 nanoseconds to 1×105 years.
The name “iron” or “iren” is Anglo-Saxon, and the symbol for iron (Fe)
is from ferrum, the Latin word for iron.
Iron is the fourth most abundant element in the Earth s crust (about 5%) and is the ninth most abundant element found in the sun and stars in the universe. The core of the Earth is believed to consist of two layers, or spheres, of iron. The inner core is thought to be molten iron and nickel mixture, and the outer core is a transition phase of iron with the molten magma of the Earth s mantle. Iron s two oxide compounds (ferrous(II) oxide FeO) and (ferric(III) oxide Fe2O3) are the third and seventh most abundant compounds found in the Earth s crust. The most common ore of iron is hematite that appears as black sand on beaches or black seams when exposed in the ground. Small amounts of iron and iron alloys with nickel and cobalt were found in meteorites (siderite) by early humans. This limited supply was used to shape tools and crude weapons. Even though small amounts of iron compounds and alloys are found in nature (iron is not found in its pure metallic state in nature), early humans did not know how to extract iron from ores until well after they knew how to smelt gold, tin, and copper ores. From these metals, they then developed bronze alloy thus the Bronze Age (about 8000 BCE). There are several grades of iron ores, including hematite (brown ferric oxide) and limonite (red ferric oxide). Other ores are pyrites, chromite, magnetite, siderite, and low-grade taconite. Magnetite (Fe3O4) is the magnetic iron mineral/ore found in South Africa, Sweden, and parts of the United States. The lodestone, a form of magnetite, is a natural magnet. Iron ores are found in many countries. Iron is found throughout most of the universe, in most of the stars, and in our sun, and it probably exists on the other planets of our solar system.
Iron is the only metal that can be tempered (hardened by heating, then quenching in wateror oil). Iron can become too hard and develop stresses and fractures. This can be corrected byannealing, a process that heats the iron again and then holds it at that temperature until thestresses are eliminated. Iron is a good conductor of electricity and heat. It is easily magnetized,but its magnetic properties are lost at high temperatures. Iron has four allotropic states. Thealpha form exists at room temperatures, while the other three allotropic forms exist at varyinghigher temperatures.Iron is the most important construction metal. It can be alloyed with many other metals tomake a great variety of specialty products. Its most important alloy is steel.An interesting characteristic of iron is that it is the heaviest element that can be formed byfusion of hydrogen in the sun and similar stars. Hydrogen nuclei can be “squeezed” in the sunto form all the elements with atomic numbers below cobalt (27Co), which includes iron. Itrequires the excess fusion energy of supernovas (exploding stars) to form elements with protonnumbers greater than iron (26Fe).
Iron is a relatively abundant element in the universe. It is found in the sun and many types of stars in considerable quantity. It has been suggested that the iron we have here on Earth may have originated in a supernova. Iron is a very difficult element to produce in ordinary nuclear reactions, such as would take place in the sun. Iron is found native as a principal component of a class of iron–nickel meteorites known as siderites, and is a minor constituent of the other two classes of meteorites. The core of the Earth, 2150 miles in radius, is thought to be largely composed of iron with about 10% occluded hydrogen. The metal is the fourth most abundant element, by weight, making up the crust of the Earth. The most common ore is hematite (Fe2O3). Magnetite (Fe3O4) is frequently seen as black sands along beaches and banks of streams. Lodestone is another form of magnetite. Taconite is becoming increasingly important as a commercial ore. Iron is a vital constituent of plant and animal life, and appears in hemoglobin. The pure metal is not often encountered in commerce, but is usually alloyed with carbon or other metals. The pure metal is very reactive chemically, and rapidly corrodes, especially in moist air or at elevated temperatures. It has four allotropic forms,or ferrites, known as α, β, γ, and δ, with transition points at 700, 928, and 1530°C. The α form is magnetic, but when transformed into the β form, the magnetism disappears although the lattice remains unchanged. The relations of these forms are peculiar. Pig iron is an alloy containing about 3% carbon with varying amounts of S, Si, Mn, and P. It is hard, brittle, fairly fusible, and is used to produce other alloys, including steel. Wrought iron contains only a few tenths of a percent of carbon, is tough, malleable, less fusible, and usually has a “fibrous” structure. Carbon steel is an alloy of iron with carbon, with small amounts of Mn, S, P, and Si. Alloy steels are carbon steels with other additives such as nickel, chromium, vanadium, etc. Iron is the cheapest and most abundant, useful, and important of all metals. Natural iron contains four isotopes. Twenty-six other isotopes and isomers, all radioactive, are now recognized.
Smelting of iron from its ore occurs in a blast furnace where carbon (coke) and limestoneare heated with the ore that results in the iron in the ore being reduced and converted tomolten iron, called “pig iron.” Melted pig iron still contains some carbon and silicon as wellas some other impurities as it collects in the bottom of the furnace with molten slag floatingatop the iron. Both are tapped and drained off. This process can be continuous since moreingredients can be added as the iron and slag are removed from the bottom of the furnace.This form of iron is not very useful for manufacturing products, given that it is brittle andnot very strong.One of the major advances in the technology of iron smelting was the development of theBessemer process by Henry Bessemer (1813–1898). In this process, compressed air or oxygenis forced through molten pig iron to oxidize (burn out) the carbon and other impurities. Steelis then produced in a forced oxygen furnace, where carbon is dissolved in the iron at very hightemperatures. Variations of hardness and other characteristics of steel can be achieved with theaddition of alloys and by annealing, quench hardening, and tempering the steel.Powder metallurgy (sintering) is the process whereby powdered iron or other metals arecombined together at high pressure without high heat to fit molded forms. This process is usedto produce homogenous (uniform throughout) metal parts.One of the most useful characteristics of iron is its natural magnetism, which it loses athigh temperatures. Magnetism can also be introduced into iron products by electrical induction. Magnets of all sizes and shapes are used in motors, atom smashers, CT scanners, and TV and computer screens, toname a few uses. Super magnets can be formed by addingother elements (see cobalt) tohigh-quality iron.Iron is an important element making up hemoglobinin the blood, which carriesoxygen to the cells of ourbodies. It is also very important as a trace element inthe diet, assisting with theoxidation of foods to produce energy. We need about10 to 18 milligrams of ironeach day, as a trace mineral.Iron is found in liver andmeat products, eggs, shellfish, green leafy vegetables,peas, beans, and whole graincereals. Iron deficiency maycause anemia (low red bloodcell count), weakness, fatigue,headaches, and shortness ofbreath. Excess iron in thediet can cause liver damage,but this is a rare condition.
Pure iron is very much a laboratory material and finds no great industrial use.
Iron is a mineral used in food fortification that is necessary for the
prevention of anemia, which reduces the hemoglobin concentra-
tion and thus the amount of oxygen delivered to the tissues. sources
include ferric ammonium sulfate, chloride, fructose, glycerophos-
phate, nitrate, phosphate, pyrophosphate and ferrous ammonium
sulfate, citrate, sulfate, and sodium iron edta. the ferric form (fe3+)
is iron in the highest valence state and the ferrous form (fe2+) is iron
in a lower valence state. the iron source should not discolor or add
taste and should be stable. iron powders produce low discoloration
and rancidity. it is used for fortification in flour, baked goods, pasta,
and cereal products.
Most iron produced today is from its oxide minerals, hematite and magnetite. The process involves reducing mineral iron with carbon in a blast furnace. There are several types of blast furnaces which vary in design anddimensions. The overall processes, however, are more or less the same. Onesuch process is outlined below:
The mixture of ore, coke and limestone is fed into the blast furnace from thetop. The materials are preheated to about 200°C in the top most zone.Hematite is partially reduced to magnetite and then to FeO by the ascendingstream of carbon monoxide formed at the bottom and mid zones of the furnaceresulting from high temperature oxidation of carbon. The ferrous oxide FeOformed at the top zone is reduced to metallic iron at about 700°C in the midzone by carbon monoxide. A hot air blast at 900°C passes through the entirefurnace for a very short time (usually for a few seconds). This prevents any gassolid reaction product from reaching equilibrium. In the temperature zone 700to 1,200°C ferrous oxide is completely reduced to iron metal by carbon monox-ide. Also, more CO is formed by oxidation of carbon by carbon dioxide. Furtherdown the furnace at higher temperatures, around 1,500°C, iron melts, drippingdown into the bottom. Also, in this temperature zone acidic silica particlesreact with basic calcium oxide produced from the decomposition of limestone,producing calcium silicate. The molten waste calcium silicate also drips downinto the bottom. In the hottest zone of the blast furnace, between 1,500 to2,000°C, some carbon dissolves into the molten iron. Also at these temperatures any remaining silicates and phosphates are reduced to silicon and phosphorus, and dissolve into the molten iron. Additionally, other tract metals suchas manganese dissolve into the molten iron. The impure iron melt containingabout 3 to 4% carbon is called “pig iron”. At the bottom, the molten waste slagfloats over the impure pig iron melt that is heavier than the slag melt andimmiscible with it. Pig iron is separated from the slag and purified for makingdifferent types of steel. Chemical reactions and processes occurring in varioustemperature zones of blast furnace are summarized below:
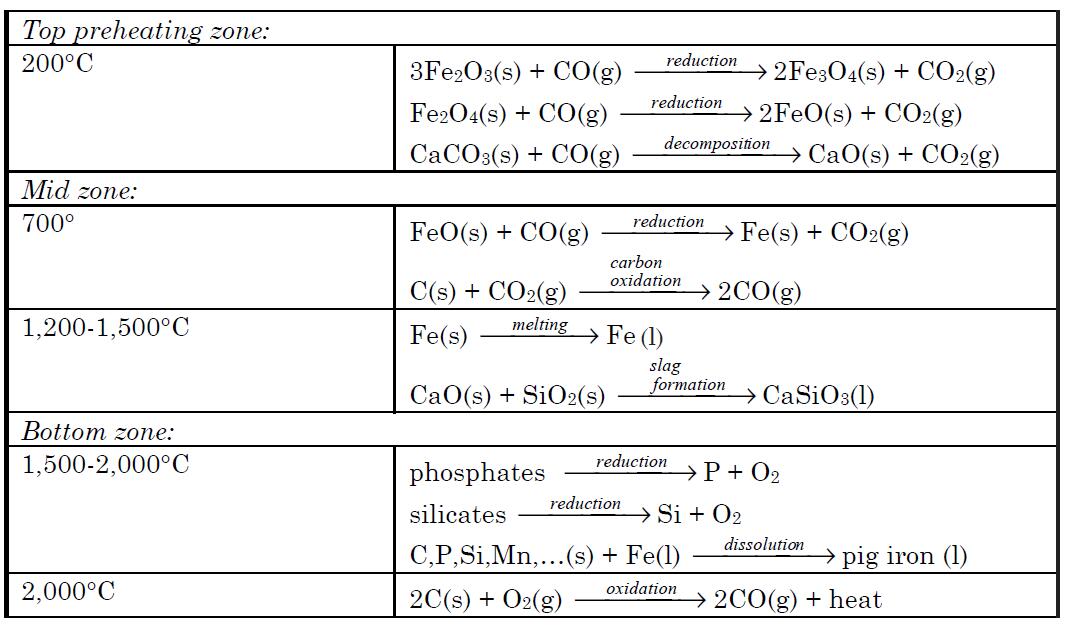
Pig iron produced in the blast furnace is purified and converted to steel ina separate furnace, known as a basic-oxygen furnace. Jets of pure oxygen gasat high pressure are blown over and through the pig iron melt. Metal impurities are converted into oxides. Part of the dissolved carbon in the impure ironmelt is converted into carbon dioxide gas. Formation of SiO2, CO2,and othermetal oxides are exothermic reactions that raise the temperature to sustainthe melt. A lime flux (CaO) also is added into the melt, which converts silicainto calcium silicate, CaSiO3,and phosphorus into calcium phosphate,Ca3(PO4)2,forming a molten slag immiscible with molten steel. The lightermolten slag is decanted from the heavier molten steel.
Iron ore reserves are found worldwide. Areas with more than
1 billion metric tons of reserves include Australia, China,
Brazil, Canada, the United States, Venezuela, South Africa,
India, the former Soviet Union, Gabon, France, Spain,
Sweden, and Algeria. The ore exists in varying grades,
ranging from 20 to 70% iron content. North America has
been fortunate in its ore deposits. There are commercially
usable quantities in 22 U.S. states and in six Canadian
provinces. In the United States the most abundant supplies,
discovered in the early 1890s, are located in the Lake Superior
region around the Mesabi Range. Other large deposits are
found in Alabama, Utah, Texas, California, Pennsylvania,
and New York. These deposits, particularly the Mesabi
Range reserves, seemed inexhaustible in the 1930s when
an average of 30 million tons of ore was produced annually
from that one range. The tremendous demand for iron ore
duringWorldWar II virtually tripled the output of the Mesabi
Range and severely depleted its deposits of high-grade ore.
The major domestic (U.S.) production is nowfrom crude iron
ore, mainly taconite, a low-grade ore composed chiefly of
hematite [FeO(OH) ·H2O] and silica found in the Great
Lakes region.
Metallic element of atomic number 26, group VIII of
the periodic table, aw 55.847, valences = 2,3; four
stable isotopes, 4 artificially radioactive isotopes.
iron: Symbol Fe. A silvery malleableand ductile metallic transition element;a.n. 26; r.a.m. 55.847; r.d.7.87; m.p. 1535°C; b.p. 2750°C. Themain sources are the ores haematite(Fe2O3), magnetite (Fe3O4), limonite(FeO(OH)nH2O), ilmenite (FeTiO3),siderite (FeCO3), and pyrite (FeS2).The metal is smelted in a blast furnaceto give impure pig iron, whichis further processed to give castiron, wrought iron, and varioustypes of steel. The pure element hasthree crystal forms: alpha-iron, stablebelow 906°C with a body-centredcubicstructure; gamma-iron, stablebetween 906°C and 1403°C with anonmagnetic face-centred-cubicstructure; and delta-iron, which isthe body-centred-cubic form above1403°C. Alpha-iron is ferromagneticup to its Curie point (768°C). The elementhas nine isotopes (mass numbers52–60), and is the fourth mostabundant in the earth’s crust. It is requiredas a trace element (see essentialelement) by living organisms.Iron is quite reactive, being oxidizedby moist air, displacing hydrogenfrom dilute acids, and combiningwith nonmetallic elements. It formsionic salts and numerous complexeswith the metal in the +2 or +3 oxidationstates. Iron(VI) also exists in theferrate ion FeO42-, and the elementalso forms complexes in which its oxidationnumber is zero (e.g. Fe(CO)5).
A gray lustrous powder. Used in powder metallurgy and as a catalyst in chemical manufacture.
Highly flammable. May react with water to give off hydrogen, a flammable gas. The heat from this reaction may ignite the hydrogen.
Iron is pyrophoric [Bretherick, 1979 p. 170-1]. A strong reducing agent and therefore incompatible with oxidizing agents. Burns in chlorine gas [Mellor 2, Supp. 1:380 1956]. Reacts with fluorine with incandescence [Mellor 13:314, 315, 1946-1947].
Iron dust from most iron compounds is harmful if inhaled and toxic if ingested. Iron dustand powder (even filings) are flammable and can explode if exposed to an open flame. Asmentioned, excessive iron in the diet may cause liver damage.
Fire may produce irritating and/or toxic gases. Contact may cause burns to skin and eyes. Contact with molten substance may cause severe burns to skin and eyes. Runoff from fire control may cause pollution.
Flammable/combustible material. May be ignited by friction, heat, sparks or flames. Some may burn rapidly with flare burning effect. Powders, dusts, shavings, borings, turnings or cuttings may explode or burn with explosive violence. Substance may be transported in a molten form at a temperature that may be above its flash point. May re-ignite after fire is extinguished.
reagent type: catalyst
core: iron
Carbonyl iron has a role as an absorber of microwave radiation. Carbonyl iron also exhibits shielding properties because of the low density and the connectivity among the fillers it provide. It is used in industries and in the synthesis of nitro-group-containing pharmaceutical ingredients.
Iron occurs rarely by itself in nature due to the ease with which
it forms compounds, especially in oxidation reactions. Many
iron compounds are water soluble, leading to potentially high
concentrations in water, especially in seawater. Iron is a necessary
component of all life and it is therefore taken up readily by
organisms from all sources.
Clean it in conc HCl, rinse in de-ionised water, then reagent grade acetone and dry it under vacuum.
Structure and conformation
Two structural types of iron occur in the solid state. At room temperature iron has a
body-centered cubic lattice (the a form). At about 910°C the a form is transformed into
the γ allotrope which has a cubic close-packed structure. Around 1390°C a body-centred
cubic lattice is reformed—the δ form. Thus the allotropy of iron is unusual in that it can
exist with the same crystal form in two distinct temperature ranges which are separated by a
range within which a different form is stable. The a and ? forms have similar lattice parameters—
the differences between them being expected in view of thermal expansion which
increases the size of the unit cell of the δallotrope.
In some adults, iron overload can be the result of a genetic
defect (idiopathic hemochromatosis) that causes malfunction of the normal homeostasis mechanism and, in turn, excessive
absorption of iron. Iron overload can also be caused by too
many blood transfusions, which results in too much iron in the
various iron-containing organs.
Recently, it has been suggested that the presence of
increased transferrin concentrations in males is associated with
an increased number of heart attacks. This must be corroborated
by further research. Excess iron can lead to diabetes
mellitus, faulty liver functions, and endocrine disturbance.
Iron is a catalyst for oxidative damage leading to lipid peroxidation.
The latest hypotheses link peroxidation to heart
disease, cancer, and accelerated aging. Iron is involved in the
Fenton reaction, which catalyzes the formation of free radicals
that cause excessive damage to cells and their components.