1,4-cyclohexanedimethanol is a white waxy solid or clear colourless viscous liquid after melting. Melting point 43°C(cis), 70°C (trans). The sublimation temperature is 160°C, miscible with water and alcohol, soluble in ketone, almost insoluble in aliphatic hydrocarbon and ether.
1,4-Cyclohexanedimethanol (CHDM) is both hard and flexible, with high TG, and offers excellent heat stability, good solubility, and good weather resistance. It can enhance the reactivity in polyester compounds, and improve the hydrolytic stability, plasticity, gloss, transparency, printability, and processing ability of the polymer.
1,4-cyclohexanedimethanol is used to make polyester fiber, polyester electrical appliances, unsaturated polyester resins, polyester glaze, polyurethane foam, as well as for the production of lubricants and hydraulic fluids.
The commercially important process for producing CHDM is the hydrogenation of dimethyl terephthalate (DMT) via dimethyl hexahydroterephthalate (DMHT) in a methanolic solution or in the molten state. The hydrogenation plant consists of two reactors. In the fifirst reactor, a continuous circulation of product DMHT and of DMT is maintained. The molten DMT is pumped into the inlet of this reactor, which operates at 30 – 48 MPa and 160 – 180 ℃ with a commercial supported Pd catalyst. Temperature control is achieved by operating at suffificiently high cross-sectional loadings of the mixture of ca. 10 % in product DMHT. This allows the radial dissipation of heat via the reactor walls and largely avoids high temperature peaks. The cooled reactor efflfluent, which contains only minor amounts of unreacted DMT, is divided: 8 – 10 parts are recycled via a pump and heat exchanger to the reactor inlet. The remaining 1-2 parts (the exact amount corresponds to the amount of fresh DMT) are fed continuously into the second reactor for the fifinal Pd-catalyzed hydrogenation.
An advantage of this process is that DMT can be hydrogenated as ca. 10 % dilute feed without handling large amounts of liquid. The yield of DMHT is typically 97 – 98 %, with methyl 4-methyl-4- cyclohexanecarboxylic acid methyl ester and some 1-hydroxymethyl-4-methylcyclohexane as main byproducts. 1,4-Bis(hydroxymethyl)cyclohexane (CHDM) is formed in the second stage of the hydrogenation.
The industrial processes use commercial copper chromite catalysts. The effects of catalyst, residence time, and temperature must be carefully adjusted in order to achieve a cis/trans ratio of 1/3 to 1/4 in the CHDM product. A constant isomer ratio is important for further processing of CHDM in polyester formation since the crystal structures of polyesters of cisand trans-CHDM differ and thus inflfluence the melting range and density of polyester fifibers.
In addition to the side products of the fifirst hydrogenation stage, 4-methyloxymethylhy-droxymethylcyclohexane and bis(4-hydroxymethylcyclohexyl) ether can be formed in the second stage of ester hydrogenation. The Eastman process avoids the formation of high-boiling compounds and thus saves cumbersome separation of side products by fractionation in vacuum. The diol is purifified by simply removing methanol and low-boiling compounds. The CHDM of fifiber quality obtained by this method is ca. 99 % pure. Pure CHDM may also be obtained by recycling waste poly(1,4-cyclohexylene dimethylene terephthalate) by fifirst cleaving the polyester in the presence of low molecular mass alcohols and then subjecting the resulting mixture to a hydrogenation analogous to that described above.
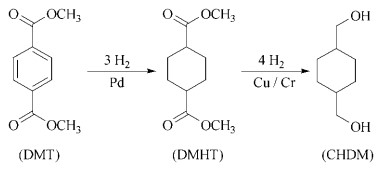
1,4-Cyclohexanedimethanol is a precursor to polyesters. It is one of the most important co-monomers for production of polyethylene terephthalate (PET), or polyethylene terephthalic ester (PETE). 1,4-Cyclohexanedimethanol has been used in the synthesis of polyketal copolymers. It was used as diol comonomer during the synthesis of polyester-carbonates based on 1,3-propylene-co-1,4-cyclohexanedimethylene succinate.
In the first step, proline-catalyzed formal [3+1+2] cycloaddition of formaldehyde, crotonaldehyde, and ethyl acrylate affords ethyl 4-formylcyclohex-3-enecarboxylate (compound 1) by a domino Mannich condensation and Diels–Alder (D–A) process.
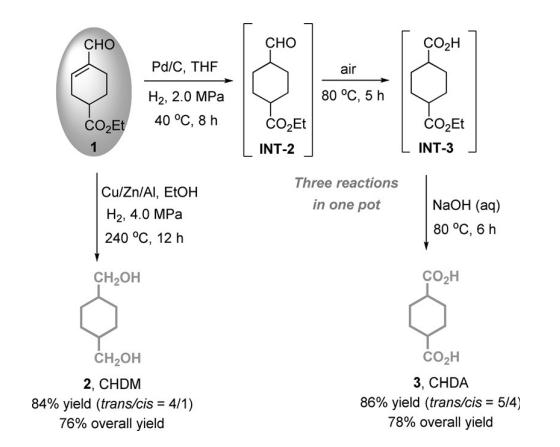
synthesis of 1,4-Cyclohexanedimethanol (CHDM) and CHDA from compound 1. Cu-based catalysts have been widely used for the hydrogenation of esters to alcohols. compound 1 can be hydrogenated to CHDM over commercially available Cu/Zn/Al catalyst. Under the optimized reaction conditions (240°C, 4.0 MPa of H2 , 12 h), a high yield (84%) of CHDM was achieved. After taking the optimized yield of compound 1 (91%) into account in the first step, the overall yield of CHDM starting from formaldehyde, crotonaldehyde, and ethyl acrylate, reached 76%.
1,4-Cyclohexanedimethanol (CHDM) undergoes the characteristic reactions of a diol with two primary hydroxyl functions. In contrast to 1,2- and 1,3-diols reactions of CHDM with aldehydes or ketones do not result in the formation of heterocyclic products, such as 1,3-dioxolanes or 1,3-dioxenanes.
Its solubility at 20 ℃ (g in 100 g solvent) in benzene is 1.1, in trichloromethane 5.7, in water 92.0, and in methanol 92.2.