Acrylonitrile is a colourless, flammable liquid. Its vapours may explode when exposed to an open flame. Acrylonitrile does not occur naturally. It is produced in very large amounts by several chemical industries in the United States, and its requirement and demand are increasing in recent years. Acrylonitrile is a heavily produced, unsaturated nitrile. It is used to make other chemicals such as plastics, synthetic rubber, and acrylic fibres. It has been used as a pesticide fumigant in the past; however, all pesticide uses have been discontinued. This compound is a major chemical intermediate used in creating products such as pharmaceuticals, antioxidants, and dyes, as well as in organic synthesis. The largest users of acrylonitrile are chemical industries that make acrylic and modacrylic fibres and high-impact ABS plastics. Acrylonitrile is also used in business machines, luggage, construction material, and manufacturing of styrene-acrylonitrile (SAN) plastics for automotive, household goods, and packaging material. Adiponitrile is used to make nylon, dyes, drugs, and pesticides.
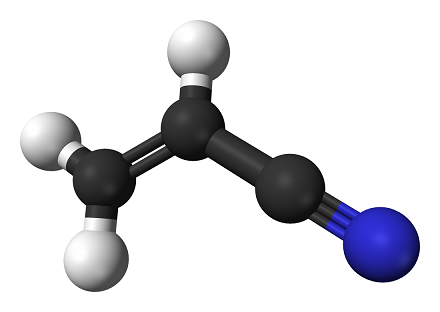
Acrylonitrile-3D-balls
On the eve of World War II, it was discovered that acrylonitrile copolymer can improve the oil resistance and solvent resistance of synthetic rubber and people began to be taken it seriously. During the war, it was developed in Germany of the manufacturing process through epoxidation of ethylene, followed by addition with hydrogen cyanide to produce cyanide ethanol, and finally dehydration. It was later developed of addition of hydrogen cyanide to acetylene under the catalysis of cuprous chloride. After 1960, it had been developed of new production process in the Ohio standard oil company, using propylene as raw material for ammoxidation reaction to obtain it. This process has led to great changes in industrial production. Owing to the availability of raw materials and the reduction in the cost, there is a sudden surge in production of acrylonitrile. In 1983, the world's annual output reached 3 million tons, of which the production amount of Ohio standard oil can account for 90%.
Acrylonitrile is easy to undergo polymerization, being able to produce polyacrylonitrile fiber (under the trade name of acrylic or bulk). Its short fiber is similar to wool, also known as artificial wool. It feels soft by hand with excellent elasticity. It can co-polymerize with vinyl acetate to generate synthetic fibers (under the commercial name of Austrian Lun). In 1950, it was first put into industrial production by the United States DuPont. The majority of acrylonitrile is used for synthetic fiber with the amount accounting for about 40~60% of the total. With copolymerization with butadiene copolymerization, it can generate oil-resistant nitrile rubber. Acrylonitrile dimerization and hydrogenation can be lead to adiponitrile, with then hydrogenation being able to obtain hexamethylene diamine, which is one of the raw materials of polyamide (nylon 66). The co-polymer of acrylonitrile and butadiene, styrene terpolymer is a high-quality engineering plastics, referred to as ABS resin.
Acrylonitrile is a clear, colorless to pale-yellow liquid with molecular formula C3H3N and molecular weight of 53.06. The yellowing color is upon exposure to light and indicate photo-alteration to saturate derivate. It is practically odorless, or with a very slight odor that may be describe as sweet, irritating, unpleasant, onion or garlic-like or pungent. Odor can only be detected above PEL. Boiling point of 77.3°C and melting point of −82 °C. The specific gravity is 0.8004 @ 25 deg C, pH is from 6.0 to 7.5 (5% aqueous solution), vapor density of 1.8 (Air=1), Vapor pressure 109 mm Hg @ 25°C. The Henry law constant is 1.38×10−4 atm cu m/mole @ 25°C.
In 1941~1942, the German Degesch Gesellsch company recommended to use acrylonitrile as a food fumigant.
Toxicity: acrylonitrile is of great toxicity to human with comparable toxicity as hydrocyanic acid. Acrylonitrile is highly toxic to insects, and is the most toxic in the main fumigant for controlling various stored grain pests.
Acrylonitrile is used alone or in combination with carbon tetrachloride and has no effect on the germination of many vegetables, grains and flower seeds, but has some damage to maize seeds. The mixture of acrylonitrile and carbon tetrachloride can be used to control the vast majority of stored cereals pests. The results showed that acrylonitrile and carbon tetrachloride, when formulated into mixture in a ratio of 1:1, can be used to control the Phthorimaea operculella Zell occurring in potato under storage without damaging the tubers.
Usage method: Because acrylonitrile and carbon tetrachloride are of high boiling point, upon atmospheric fumigation, in order to be quickly evaporated, it was developed of a simple method which uses cotton cord core to pass through the shallow iron disk bottom. During the beginning of the fumigation, inject a liquid fumigant into the dish and then blow the air through the fan to the cotton core until the evaporation is complete.
Acrylonitrile is primarily used in the manufacture of acrylic and modacrylic fibers. It is also used as a raw material in the manufacture of plastics (acrylonitrile-butadiene-styrene and styrene-acrylonitrile resins), adiponitrile, acrylamide, and nitrile rubbers and barrier resins. A mixture of acrylonitrile and carbon tetrachloride was used as a pesticide in the past; however, all pesticide uses have stopped. Acrylonitrile is a commercially important industrial chemical that has been used extensively since 1940s with the rapid expansion of the petrochemical industry.
The production of ABS and SAN resins consumes the second largest quantity of acrylonitrile. The ABS resins are produced by grafting acrylonitrile and styrene onto polybutadiene or a styrene–butadiene copolymer and contain about 25 wt% acrylonitrile. These products are used to make components for automotive and recreational vehicles, pipe fittings, and appliances. The SAN resins are styrene–acrylonitrile copolymers containing 25–30 wt% of acrylonitrile. The superior clarity of SAN resin allows it to be used in automobile instrument panels, for instrument lenses and for houseware items (Langvardt, 1985; Brazdil, 1991).
Acrylonitrile is a colorless, flammable liquid. Its vapors may explode when exposed to an
open flame. Acrylonitrile does not occur naturally. It is produced in very large amounts
by several chemical industries in the United States and its requirement and demand has
increased in recent years. The largest users of acrylonitrile are chemical industries that make
acrylic and modacrylic fi bers, high impact acrylonitrile-butadiene-styrene (ABS) plastics.
Acrylonitrile is also used in business machines, luggage, and construction material, in the
manufacturing of styrene-acrylonitrile (SAN) plastics for automotive and household goods,
and in packaging material. Adiponitrile is used to make nylon, dyes, drugs, and pesticides.
Acrylonitrile is used in the production of acrylic fibers, resins, and surface coating; as an intermediate in the production of pharmaceuticals and dyes; as a polymer modifier; and as a fumigant. It may occur in fire-effluent gases because of pyrolyses of polyacrylonitrile materials. Acrylonitrile was found to be released from the acrylonitrile–styrene copolymer and acrylonitrile–styrene–butadiene copolymer bottles when these bottles were filled with food-simulating solvents such as water, 4% acetic acid, 20% ethanol, and heptane and stored for 10 days to 5 months (Nakazawa et al. 1984). The release was greater with increasing temperature and was attributable to the residual acrylonitrile monomer in the polymeric materials.
Acrylonitrile is produced in commercial quantities almost exclusively by the vapor-phase catalytic propylene ammoxidation process developed by Sohio.
C3H6 + NH3 + 2/3O2→ C3H3N +3H2O
The one-step, fluid bed Acrylonitrile manufacturing process was developed by scientists of The Standard Oil Company (Sohio), one of INEOS's predecessors in the U.S. in the 1950s. Today, over 95 percent of the world's Acrylonitrile is manufactured using INEOS's exclusive technology.
ChEBI: Acrylonitrile is a nitrile that is hydrogen cyanide in which the hydrogen has been replaced by an ethenyl group. It is very toxic and irritant but is also a sensitizer. It caused both irritant and allergic contact dermatitis in a production manufacture.
Highly flammable. Soluble in water.
ACRYLONITRILE produces poisonous hydrogen cyanide gas on contact with strong acids or when heated to decomposition. Reacts violently with strong oxidizing agents (dibenzoyl peroxide, di-tert-butylperoxide, bromine) [Sax, 9th ed., p. 61]. Rapidly ignites in air and forms explosive mixtures with air. Polymerizes violently in the presence of strong bases or acids. Underwent a runaway reaction culminating in an explosion on contact with a small amount of bromine or solid silver nitrate [Bretherick, 5th ed., 1995, p. 404].
Acrylonitrile is a highly toxic compound, an irritant to the eyes and skin, mutagenic, teratogenic, and causes cancer in test animals.
Acrylonitrile is a moderate to severe acute toxicant via inhalation, oral intake, dermal absorption, and skin contact. Inhalation of this compound can cause asphyxia and headache. Firefighters exposed to acrylonitrile have reported chest pains, headache, shortness of breath, lightheadedness, coughing, and peeling of skin from their lips and hands (Donohue 1983). These symptoms were manifested a few hours after exposure and persisted for a few days. Inhalation of 110 ppm for 4 hours was lethal to dogs. In humans, inhalation of about 500 ppm for an hour could be dangerous. The toxicity symptoms in humans from inhaling high concentrations of acrylonitrile were somnolence, diarrhea, nausea, and vomiting (ACGIH 1986).
Flammability and Explosibility
Not classified
Acrylonitrile is a raw material used extensively in industry,
mainly for acrylic and modacrylic fibers, acrylonitrile-butadiene-styrene
and styrene-acrylonitrile resins,
adiponitrile used in nylon’s synthesis, for nitrile rubber,
and plastics. It is also used as an insecticide. This very
toxic and irritant substance is also a sensitizer and caused
both irritant and allergic contact dermatitis in a production
manufacturer.
An industrial carcinogen that is a multisite carcinogen in rats and possibly carcinogenic to humans.
Acrylonitrile is used in the manufacture of synthetic fibers, polymers, acrylostyrene plastics, acrylonitrile butadiene styrene plastics, nitrile rubbers, chemicals, and adhesives. It is also used as a pesticide. In the past, this chemical was used as a room fumigant and pediculicide (an agent used to destroy lice).
Acrylonitrile is reasonably anticipated to be a human carcinogenbased on sufficient evidence of carcinogenicity from studies in experimental animals.
Work with acrylonitrile
should be conducted in a fume hood to prevent exposure by inhalation, and splash
goggles and impermeable gloves should be worn at all times to prevent eye and skin
contact. Acrylonitrile should be used only in areas free of ignition sources.
Containers of acrylonitrile should be stored in secondary containers in the dark in
areas separate from oxidizers and bases.
UN1093 Acrylonitrile, stabilized, Hazard Class 3; Labels: 3 Flammable liquids, 6.1-Poisonous materials
Wash acrylonitrile with dilute H2SO4 or dilute H3PO4, then with dilute Na2CO3 and water. Dry it with Na2SO4, CaCl2 or (better) by shaking with molecular sieves. Fractionally distil it under N2. It can be stabilised by adding 10ppm tert-butyl catechol. Immediately before use, the stabilizer can be removed by passage through a column of activated alumina (or by washing with 1% NaOH solution if traces of water are permissible in the final material), followed by distillation. Alternatively, shake it with 10% (w/v) NaOH to extract inhibitor, and then wash it in turn with 10% H2SO4, 20% Na2CO3 and distilled water. Dry for 24hours over CaCl2 and fractionally distil under N2 taking fraction boiling at 75.0-75.5oC (at 734mm). Store it with 10ppm tert-butyl catechol. Acrylonitrile is distilled off when required. [Burton et al. J Chem Soc, Faraday Trans 1 75 1050 1979, Beilstein 2 IV 1473.]
Acrylonitrile is both readily volatile in air and highly soluble in water. These characteristics determine the behavior of acrylonitrile in the environment. The principal pathway leading to the degradation of acrylonitrile in air is photooxidation, mainly by reaction with hydroxyl radicals (OH). Acrylonitrile may also be oxidized by other atmospheric components such as ozone and oxygen. Very little is known about the nonbiologically mediated transformation of acrylonitrile in water. It is oxidized by strong oxidants such as chlorine used to disinfect water. Acrylonitrile is readily degraded by aerobic microorganisms in water.
Acrylonitrile is reactive with, and must be kept away from, strong oxidizers, especially bromine. Use extreme care to keep Acrylonitrile away from strong bases, strong acids, copper, copper alloys, ammonia and amines. Contact with these chemicals can cause a chemical reaction resulting in a fire or explosion. Chemical compatibility should also be determined before Acrylonitrile comes in contact with any other chemical.
The initial threshold screening level for acrylonitrile (CAS # 107-13-1) is 2 μg/m3 based on an annual averaging time.
Consult with environmental regulatory agencies for guidance on acceptable disposal practices. Generators of waste containing this contaminant (≥100 kg/mo) must conform with EPA regulations governing storage, transportation, treatment, and waste disposal. Incineration with provision for nitrogen oxides removal from effluent gases by scrubbers or afterburners. A chemical disposal method has also been suggested involving treatment with alcoholic NaOH; the alcohol is evaporatedand calcium hypochlorite added; after 24 hours the product is flushed to the sewer with large volumes of water. Recovery of acrylonitrile from acrylonitrile process effluents is an alternative to disposal.