Production of anthracene
Anthracene was first discovered in coal tar by Jean B.A Dumas and Auguste Laurent in 1832. The importance of anthracene for industrial aromatic chemistry began with the synthesis of the dyestuff alizarin by Carl Graebe and Carl Th. Liebermann, as well as by William H. Perkin in 1868, replacing the natural dye produced from madder. Anthraquinone dyestuffs have remained the most important class of dyes, alongside azo-dyes, since the beginning of the chemistry of synthetic dyestuffs.
From the time of the first alizarin synthesis, anthraquinone has been the most
versatile anthracene derivative. This applies both for dye production and for the
more recent applications of anthraquinone, as an additive (redox-catalyst) in
wood pulping, and as a hydrogen carrier in H2O2 production.
Production of anthracene
While it is possible to recover the bicyclic naphthalene from pyrolysis products of
coal and petroleum-derived raw materials, the tricyclic anthracene can be isolated
only from high-temperature coal tar, since anthracene is present only in small
amounts in other pyrolysis products and in the residues of catalytic hydrocarbon
conversion.
Synthetic production of anthracene has gained no industrial significance so far,
since sufficient quantities are present in coal tar; in theory, supplies of around
150,000 tpa of anthracene are available to meet a demand of some 20,000 tpa.
The first stage in the production of anthracene is the recovery of a 25 to 30%
anthracene concentrate by crystallization, which can be carried out in two stages
to increase the yield. The crystallizate, known as 'anthracene cake', is generally
concentrated to around 50% by vacuum distillation. The main co-boiling compound of '50's anthracene' is henanthrene while carbazole is reduced to below 2%. Subsequent refining to yield 'pure anthracene', containing over 95%, is normally achieved by recrystallization in polar solvents, such as acetophenone, mixtures of cyclohexanol/ cyclohexanone or N-methylpyrrolidone; in addition, distillation or azeotropic distillation with ethylene glycol can be used for purification.
The quality of anthracene obtained by this method is sufficient for the manufacture of anthraquinone by the usual processes. Because of hydrogen transfer during
coal tar refining, the fore-runnings which arise during the distillation of the
anthracene cake are enriched with 9,10-dihydroanthracene, which can be converted into anthracene by oxidation with air. This anthracene, recoverable by subsequent crystallization, is distinguished by an exceptionally low nitrogen content.
Figure below shows the flow diagram for recovery of pure anthracene from
anthracene oil, by the combined application of crystallization and distillation.
Figure: Flow diagram for production of anthracene from anthracene oil
In spite of the adequate availability of anthracene from coal tar, processes have
been developed to synthesize anthracene from phenanthrene, which is present in
coal tar in higher concentrations, or from diphenylmethane.
In the Bergbau-Forschung process, phenanthrene is first hydrogenated to
sym-octahydrophenanthrene, then converted to sym-octahydroanthracene, and
finally dehydrogenated.
This synthesis, in common with the production of anthracene based on diphenylmethane by Friedel-Crafts reaction and dehydrogenation, has had no industrial
significance to date.
World production of anthracene from coal tar is around 20,000 tpa. RillgerswerkelWest Germany, with around 8,000 tpa and Nippon Steel Chemical/Japan,
with around 3,000 tpa are the major producers.
The industrial importance of anthracene consists mainly in its use as a raw
material in the production of anthraquinone; small amounts are used in production of the tranquilizer benzoctamine, which is produced from anthracene and
acrolein in a Diels-Alder reaction, followed by reductive amination of the aldehyde with methylamine.
A new application for anthracene could develop with the increasing importance
of hydrogen as a fuel, in the form of magnesium hydride. Magnesium hydride
contains 150 g hydrogen per liter, which is released on heating to 250 to 300 DC. A
metalorganic complex of magnesium with anthracene is an intermediate stage in
the synthesis of magnesium hydride. This complex is produced by the reaction of
pure magnesium with anthracene in tetrahydrofuran, at ambient temperature.
You may like
Related articles And Qustion
See also
Lastest Price from Anthracene manufacturers
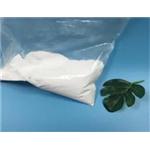
US $9.00/KG2024-05-29
- CAS:
- 120-12-7
- Min. Order:
- 1KG
- Purity:
- 99.50%
- Supply Ability:
- 50000tons
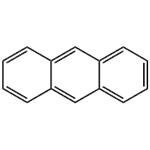
US $50.00-1.00/KG2024-03-25
- CAS:
- 120-12-7
- Min. Order:
- 1KG
- Purity:
- 99%
- Supply Ability:
- g-kg-tons, free sample is available