Naphthalene - production and uses
Naphthalene was first isolated from coal tar in 1819 by Alexander Garden; it represents about 10% of this complex mixture of aromatics. The industrial importance of naphthalene dates from the latter half of the last century, owing mainly to the ease with which it can be converted into sulfonic acids and thence also to the naphthols, for use as dyestuffs intermediates.
Uses
The development of synthetic dyestuffs provided further impetus for advances in naphthalene chemistry. Towards the end of the last century, its oxidation into phthalic anhydride (PA) attained particular importance as a step in a successful route for the economical synthesis of indigo. In the 20th century, the classic uses of naphthalene have been extended into new areas, for example, the development of the naphthol AS dyes from the parent naphthols, and the production of PAbased plasticizers and pesticides. The most recent developments iIi the field of industrial naphthalene chemistry concern the production of alkylnaphthalenederivatives as solvents for use in carbonless copy papers, as well as the manufacture of naphthoquinone for the synthesis of anthraquinone.The main uses of naphthalene in Western Europe, Japan and the USA. Although in Japan and the USA the main use of naphthalene is the production of phthalic anhydride, in Western Europe naphthalene is used in large quantities for the production of dyestuffs and tanning agents, as well as for surface-active compounds.Refined coal-derived naphthalene (crystallization point above 80 Qq, produced by crystallization or sublimation, has a worldwide application for some 30,000 t as fumigants (moth balls). In order to obtain color-stability, this grade of naphthalene requires a particularly low content of unsaturated co-products (indenes).
Although fonnerly commonly used as solvents, transfonner oils and chemical intennediates, the chloronaphthalenes are now of little commercial significance, because of their toxicity and environmental persistence.
Production
Coal tar is the traditional feedstock for the recovery of naphthalene. The introduction of new cracking processes in the last decades has given rise to the availability of petroleum-based raw materials. In addition to coal-derived naphthalene, petroleum- derived naphthalene has been recovered since 1961 - predominantly in the USA - by dealkylation of the residues of ethylene production and of reformingand cat-cracker fractions which are rich in aromatics.
The worldwide production of petroleum-derived naphthalene has been declining in the last decade, representing presently only around 5% of the total, since adequate supplies of coalbased naphthalene are available. Because of its high aromaticity, coal tar offers the most suitable source of naphthalene. In coal tar refining, rectification is used to produce a naphthalene fraction which, depending on the separation efficiency of the naphthalene column, can have a naphthalene content rising to over 90%.
Plot of crystallizing point versus naphthalene content of coal tar-based naphthalene fractions
The crystallizing point of a 'technical' naphthalene fraction from the primary distillation may be as high as 76°C, corresponding to a naphthalene content above 90%. To achieve further purification, it is necessary to separate the naphthalene from other components having similar boiling points. The proposed end-use for the product determines the extent of refining which is required. A distinction is made between 'technical' grades of naphthalene, which have crystallization points of 78.0, 78.5 and 79.0 °C (corresponding to a naphthalene content of 95 to 98%) and 'refined' naphthalene, with a crystallization point of over 79.6 °C, representing a naphthalene content in excess of 98.7%.
For the production of 'technical' naphthalene (crystallization point 78.5 ℃) a redistillation of the naphthalene oil using columns with approx. 80 trays and reflux ratios of from 7 to 10:1 is sufficient. Phenols are generally extracted from the naphthalene oil before distillation, using a 15 to 40% sodium hydroxide solution. Figure in below shows the process diagram for the distillation of a naphthalene oil fraction to recover naphthalene with a crystallization point of 78.5 ℃. The pre-column is operated under atmospheric conditions, while the main column operates at a slight overpressure, to achieve optimum heat economy.
Production of 'technical' naphthalene (crystallizing point ca.78.5 ℃) by distillation
Refined naphthalene, with a crystallization point above 79.6 ℃, is usually obtained by crystallization or hydrogenation. The choice of process is made on economic grounds, especially the price of hydrogen, and on the required level of sulfur in the refined naphthalene. Crystallization is characterized by high naphthalene yields and favorable energy costs; high yields are also favored by a high concentration of naphthalene in the feedstock. However, the sulfur content of coalderived naphthalene cannot be reduced below 300-400 ppm by crystallization processes within the framework of reasonable economics. A sulfur content below 100 ppm may be obtained by hydrorefining, but this process is associated with the disadvantage of loss of naphthalene through the formation of 1,2,3,4-tetrahydronaphthalene (tetralin) and pyrolysis products such as gases and pitch-like residues resulting from the application of elevated temperatures.
You may like
Related articles And Qustion
Lastest Price from Naphthalene manufacturers
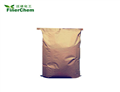
US $0.00/Kg/Bag2025-04-21
- CAS:
- 91-20-3
- Min. Order:
- 1KG
- Purity:
- 99%
- Supply Ability:
- 500mt/year
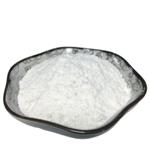
US $0.00/KG2025-03-21
- CAS:
- 91-20-3
- Min. Order:
- 1KG
- Purity:
- 99%
- Supply Ability:
- 50000KG/month