Add bisphenol A and epichlorohydrin in the amount of 1:4 into a three-necked flask equipped with a reflux device, place it in a constant-temperature oil bath, melt it with 70 °C of heat, and dropwise 28.57% aqueous sodium hydroxide solution with a dropping funnel, in which the ratio of the amount of sodium hydroxide and bisphenol A is 4:1. When dropping is completed within half an hour, heat it for 12-24 hours under temperature 70-80°C。 Stop the heating after bisphenol A is completely disappeared validated by TLC method. Cool the mixture to room temperature; add extractant toluene/water (volume ratio 2:1) and stir it at room temperature for half an hour. Transfer to a pear-shaped separatory funnel to separate the liquid, continue washing and separating with deionized water until the solution turns to neutral from alkaline. Distillation and vacuum distillation are used to remove toluene and unreacted epichlorohydrin, respectively. Use a solvent mixture of petroleum ether and ethyl acetate (volume ratio 3:1) a developing solvent to purify it by column chromatography according to the above procedure to obtain DGEBA.
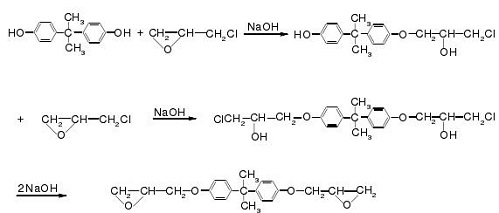
This process, also known as a one-step process, is commonly used for the preparation of low and medium molecular weight bisphenol A epoxy resins.
When the low-molecular-weight bisphenol A epoxy resin is continuously reacted with bisphenol A, the obtained bisphenol A epoxy resin has a high polymerization with a relative molecular mass 1400 or more. This is called a two-step method. When the number-average molecular weight is less than 400, the main component is bisphenol A diglycidyl ether (DGEBA, relative molecular weight 340). To fix the amount of fixed bisphenol A and make excess epichlorohydrin can obtain DGEBA. The reaction process is as follows:
As can be seen from above, the product is bisphenol A diglycidyl ether when there is sufficient epichlorohydrin and enough sodium hydroxide as the catalyst. Excessive amounts of bisphenol A generate linear high molecular compounds with hydroxyl-, etherand epoxy-terminated groups. The internal rotation function of the ether bond increases the flexibility of the molecule, and the hydroxyl group enhances the chemical reactivity and the bonding ability, the epoxy group cross-links molecules into a three-dimensional network structure by reacting with a curing agent. The performance represented by each part of the Bisphenol A-type epoxy resin is shown here: