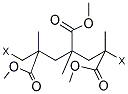
Poly(methyl methacrylate)
- Product NamePoly(methyl methacrylate)
- CAS9011-14-7
- MF(C5H8O2)x
- MW100.12
- EINECS618-466-4
- MOL File9011-14-7.mol
Chemical Properties
Melting point | 150 °C |
Boiling point | 108 °C |
Density | 1.188 g/mL at 25 °C |
Tg | 115 |
Tg | 88 |
refractive index | n |
Flash point | 250 °C |
storage temp. | 2-8°C |
solubility | alcohols and aliphatic hydrocarbons: insoluble |
form | powder |
color | White |
Specific Gravity | 1.188 |
Water Solubility | Soluble in tetrahydrofuran, toluene, cyclohexanone, ethyl acetate and chloroform. Insoluble in water, alcohols and aliphatic hydrocarbons. |
Stability | Stable. Combustible. Incompatible with strong oxidizing agents. |
LogP | 1.346 (est) |
CAS DataBase Reference | 9011-14-7 |
IARC | 3 (Vol. 19, Sup 7) 1987 |
EPA Substance Registry System | Methyl methacrylate homopolymer (9011-14-7) |
Safety Information
Hazard Codes | Xn |
Risk Statements | 20/22 |
Safety Statements | 36-24/25-22 |
WGK Germany | 3 |
RTECS | TR0400000 |
Autoignition Temperature | 580 °F |
TSCA | Yes |
HS Code | 39061000 |
MSDS
Provider | Language |
---|---|
ACROS | English |
SigmaAldrich | English |
ALFA | English |
Usage And Synthesis
Poly (methyl methacrylate) (PMMA), having the IUPAC name of poly [1-(methoxy carbonyl)- 1-methyl ethylene] from the hydrocarbon standpoint, and poly (methyl 2-methylpropenoate) from the ester standpoint, is a synthetic polymer from the methyl methacrylate monomer as illustrated in Figure 1.[1] PMMA was discovered in the early 1930s by British chemists, Rowland Hill and John Crawford, followed by its first application by a German chemist, Otto Rohm, in 1934.[2] PMMA is an optically clear (transparent) thermoplastic, and it is widely used as a substitute for inorganic glass, because it shows high impact strength, is lightweight, shatter-resistant, and exhibits favorable processing conditions.[3] Outstanding properties include weather resistance and scratch resistance. The presence of the adjacent methyl group (CH3) in the polymer structure prevents it from packing closely in a crystalline fashion, and from rotating freely around the C-C bonds. This is why PMMA was found to be an amorphous thermoplastic. The first major application of the polymer took place during World War II, when PMMA was used as aircraft windows and bubble canopies for gun turrets.
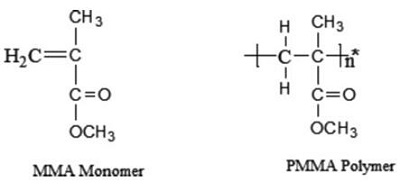
Figure 1 the chemical structure of PMMA
PMMA is a promising polymer for applications in optical, pneumatic actuation, sensor, analytical separation, and conductive devices.[4–8] Other applications include the use of PMMA in biomedical applications, polymer electrolytes, polymer viscosity, and drug delivery using electro-diffusion or electro-osmotic flow.[9–13] Due to its compatibility and easy processing as a polymer moiety, PMMA with carbon nanotubes or other inorganic materials plays an important role in the development of nanotechnology. Wang et al., in the preparation of carbon nanotube polymer composites, used poly (styrene-co-acrylonitrile) with poly (methyl methacrylate)-g-multi walled carbon nanotubes.[14]
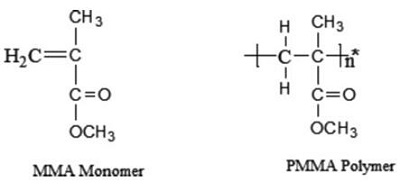
Figure 1 the chemical structure of PMMA
PMMA is a promising polymer for applications in optical, pneumatic actuation, sensor, analytical separation, and conductive devices.[4–8] Other applications include the use of PMMA in biomedical applications, polymer electrolytes, polymer viscosity, and drug delivery using electro-diffusion or electro-osmotic flow.[9–13] Due to its compatibility and easy processing as a polymer moiety, PMMA with carbon nanotubes or other inorganic materials plays an important role in the development of nanotechnology. Wang et al., in the preparation of carbon nanotube polymer composites, used poly (styrene-co-acrylonitrile) with poly (methyl methacrylate)-g-multi walled carbon nanotubes.[14]
PMMA can be obtained from its monomer using different techniques of polymerization. The monomer undergoes polymerization using the common methods of free radical and anionic initiations by bulk, solution, suspension, and emulsion techniques. [15] Following the discovery of a new technique of polymerization by Krzysztof Matyjaszewski in 1995[16] called Atom Transfer Radical Polymerization (ATRP), Matyjaszewski et al. successfully polymerized the monomer of methyl methacrylate (MMA) to produce PMMA as a living polymer with 80% conversion, poly-dispersity as low as 1.1, and an Mn of 20,000 in a few hours.[17]
PMMA is one of the amorphous polymers that belong to the acrylate family. It is a clear, colorless polymer with a glass transition temperature range of 100 degree to 130 degree, and a density of 1.20 g/cm3 at room temperature. This polymer melts at 130 degree, with a water absorptivity of 0.3%, moisture absorption at equilibrium of 0.3 to 0.33%, and a linear shrinkage mold of 0.003 to 0.0065 cm/cm[18-20].
PMMA is among the polymers that have high resistance to sunshine exposure because it has a small variation under the effect of UV-radiation. It has very good thermal stability, and is known to withstand temperatures as high as 100 degree and as low as 70 degree.
It also possesses very good optical properties, with a refractive index of 1.490, and a good degree of compatibility with human tissue.[18, 19]
PMMA is an organic polymer, and its solubility is expected to be governed by “like-dissolve-like,” with polarity playing a major role. PMMA shows little deviation, as its solubility is more complex, starting with swelling in the solvent and the subsequent formation of a very soft layer on its surface. This is then followed by diffusion of the solvent into the whole polymer before it gives a homogenous solution with the solvent. This is the reason why PMMA takes a few minutes before it is dissolved completely, even if it is in its best solvent.
PMMA hydrolyzed completely with sulfuric acid (H2SO4) to become poly (methacrylic acid) (PMAA). Hydrochloric acid and hydro-iodic acid are capable of hydrolyzing PMMA, but at a slow rate when compared to sulfuric acid[21]. PMMA has a predominantly elemental composition of carbon and hydrogen. Therefore, it is liable to undergo an exothermic combustion reaction to yield gaseous products (CO2, CO, H2O,) and energy like any other hydrocarbon. The thermal decomposition of PMMA has been extensively studied in the absence of oxygen. The decomposition temperature varies, depending on the approach used in the synthesis of the polymer. Radically polymerized PMMA containing terminal C-C bonds decompose at a temperature of 220 degree with simple mechanisms of monomer repeat units bond scission and C-C bond random scission [18].
PMMA is among the polymers that have high resistance to sunshine exposure because it has a small variation under the effect of UV-radiation. It has very good thermal stability, and is known to withstand temperatures as high as 100 degree and as low as 70 degree.
It also possesses very good optical properties, with a refractive index of 1.490, and a good degree of compatibility with human tissue.[18, 19]
PMMA is an organic polymer, and its solubility is expected to be governed by “like-dissolve-like,” with polarity playing a major role. PMMA shows little deviation, as its solubility is more complex, starting with swelling in the solvent and the subsequent formation of a very soft layer on its surface. This is then followed by diffusion of the solvent into the whole polymer before it gives a homogenous solution with the solvent. This is the reason why PMMA takes a few minutes before it is dissolved completely, even if it is in its best solvent.
PMMA hydrolyzed completely with sulfuric acid (H2SO4) to become poly (methacrylic acid) (PMAA). Hydrochloric acid and hydro-iodic acid are capable of hydrolyzing PMMA, but at a slow rate when compared to sulfuric acid[21]. PMMA has a predominantly elemental composition of carbon and hydrogen. Therefore, it is liable to undergo an exothermic combustion reaction to yield gaseous products (CO2, CO, H2O,) and energy like any other hydrocarbon. The thermal decomposition of PMMA has been extensively studied in the absence of oxygen. The decomposition temperature varies, depending on the approach used in the synthesis of the polymer. Radically polymerized PMMA containing terminal C-C bonds decompose at a temperature of 220 degree with simple mechanisms of monomer repeat units bond scission and C-C bond random scission [18].
Biomedical
PMMA has been used in the area of biomedical applications, which involves the preparation of bone cements for drug delivery/release and cranioplasty. The qualities that made the polymer a potential material for these applications include: non-toxicity, less cost, easy processability, compatibility, minimal inflammatory reactions with tissues, and greater fracture resistance, especially when used in cranioplasty.
PMMA has also been used to widen the applications of chitosan in various fields that include biomedical and pharmaceutical applications. Zuhair et al. reported the successful grafting of a PMMA/chitosan blend. The results indicated an increase in the mechanical properties, such as tensile strength and flexural modulus. The degradation, porosity, and water absorbency of the blend in synthetic body fluid (SBF) with a pH of 7.4 increased with an increase in the chitosan percentage and immersion time in SBF. These behaviors exhibited by the PMMA/chitosan blend illustrate its potentials for drug release applications[22].
Molecular Separation
Molecular separations in chemistry can be achieved in an advanced way by the use of chromatographic techniques, which involve the use of a stationary phase (inert solid support) and mobile phase (usually solvent or mixture of solvents). The common solid supports used are inorganic materials such as silica and alumina, but they have low patronage due to their disadvantages in separating some organic molecules, and limited modifications for maximum efficiency. Therefore, both natural and synthetic polymers have recently been used to replace the inorganic materials. PMMA is the most promising synthetic polymer for applications in molecular separation due to its low cost, compatibility, ease of modification, and processability[7, 23].
Optical applications
Optical science is relevant and studied in many disciplines, including engineering, medicine, pure science, and astronomy. Practical applications are found in lenses, microscopes, lasers, fibers, and polymers, to name a few. The optical activity of any material is the result exhibited by that material when interacting with light and the refractive index is the measure of that activity. The optical applications of PMMA are due to its refractive index, good resistance to UV light, chemical durability, and good mechanical properties.
Organic polymers are usually cheap, lightweight, and easily processed substrates, and are therefore good for immobilizing semiconductors for heterogeneous photocatalytic applications. Camara et al. revealed the investigation of eleven synthetic polymers susceptible to coating with TiO2 for exposure to solar radiation, with and without the TiO2 layer, for 150 days to study the weathering. They observed that only the PMMA retains good optical and mechanical properties of the Titania after natural weathering. Therefore, PMMA is the best candidate for the immobilization of TiO2 for photocatalytic treatment applications[24].
Polymer conductivity and electrolytes
Most polymers are electrical insulators. However, conducting polymers can be prepared using an insulating polymer and electrically conductive fillers called dopants. The electrical properties of PMMA doped with conducting materials under various experimental conditions including photo-induced changes, has been studied. PMMA was used as an organic insulator, while the PVA-PAA-glycerol was a semiconducting polymer. Aluminum electrodes were used as bottom and top electrodes for the fabricated devices. Finally, organic memory devices were prepared based on the Au-PtAg nanoparticles as charge storage elements. Herein, PMMA was used as the organic insulator[25].
A polymer electrolyte membrane for battery application must play the following roles: must enable positive ion transport such as Li+ between the electrodes, must block the electron transport, and must be rigid to prevent direct contact between the electrodes[26]. The application of PMMA in the polymer electrolyte was due to the amorphous nature for porosity’s sake and the mechanical strength it has for the provision of the rigidity to the polymer electrolyte membrane.
Sensor application
In search of the production of a quasi-solid-state dye-sensitized solar cell (DSSC) using a high conductivity polymer gel electrolyte, a suitable polymeric material was needed to be a host matrix in the composite. Therefore, PMMA was found to be a good and compatible polymer for this purpose. This was attributed to its mechanical strength, compatibility, and optical clarity[27].
Solar and nanotechnology applications
Due to the wider application of nanocomposites in the field of nanotechnology, many researchers focused their attention on nanocomposites, their fabrication, and applications. Perween et al. reported the use of PMMA and graphite to fabricate plastic chip electrodes (PCEs) via a simple solution casting method. This characterization was made using microscopy (SEM and AFM) as well as thermal properties (TGA), and mechanical and electrical properties. The fabricated electrode was economically inexpensive, multipurpose, and dispensable for various applications[28].
PMMA has been used in the area of biomedical applications, which involves the preparation of bone cements for drug delivery/release and cranioplasty. The qualities that made the polymer a potential material for these applications include: non-toxicity, less cost, easy processability, compatibility, minimal inflammatory reactions with tissues, and greater fracture resistance, especially when used in cranioplasty.
PMMA has also been used to widen the applications of chitosan in various fields that include biomedical and pharmaceutical applications. Zuhair et al. reported the successful grafting of a PMMA/chitosan blend. The results indicated an increase in the mechanical properties, such as tensile strength and flexural modulus. The degradation, porosity, and water absorbency of the blend in synthetic body fluid (SBF) with a pH of 7.4 increased with an increase in the chitosan percentage and immersion time in SBF. These behaviors exhibited by the PMMA/chitosan blend illustrate its potentials for drug release applications[22].
Molecular Separation
Molecular separations in chemistry can be achieved in an advanced way by the use of chromatographic techniques, which involve the use of a stationary phase (inert solid support) and mobile phase (usually solvent or mixture of solvents). The common solid supports used are inorganic materials such as silica and alumina, but they have low patronage due to their disadvantages in separating some organic molecules, and limited modifications for maximum efficiency. Therefore, both natural and synthetic polymers have recently been used to replace the inorganic materials. PMMA is the most promising synthetic polymer for applications in molecular separation due to its low cost, compatibility, ease of modification, and processability[7, 23].
Optical applications
Optical science is relevant and studied in many disciplines, including engineering, medicine, pure science, and astronomy. Practical applications are found in lenses, microscopes, lasers, fibers, and polymers, to name a few. The optical activity of any material is the result exhibited by that material when interacting with light and the refractive index is the measure of that activity. The optical applications of PMMA are due to its refractive index, good resistance to UV light, chemical durability, and good mechanical properties.
Organic polymers are usually cheap, lightweight, and easily processed substrates, and are therefore good for immobilizing semiconductors for heterogeneous photocatalytic applications. Camara et al. revealed the investigation of eleven synthetic polymers susceptible to coating with TiO2 for exposure to solar radiation, with and without the TiO2 layer, for 150 days to study the weathering. They observed that only the PMMA retains good optical and mechanical properties of the Titania after natural weathering. Therefore, PMMA is the best candidate for the immobilization of TiO2 for photocatalytic treatment applications[24].
Polymer conductivity and electrolytes
Most polymers are electrical insulators. However, conducting polymers can be prepared using an insulating polymer and electrically conductive fillers called dopants. The electrical properties of PMMA doped with conducting materials under various experimental conditions including photo-induced changes, has been studied. PMMA was used as an organic insulator, while the PVA-PAA-glycerol was a semiconducting polymer. Aluminum electrodes were used as bottom and top electrodes for the fabricated devices. Finally, organic memory devices were prepared based on the Au-PtAg nanoparticles as charge storage elements. Herein, PMMA was used as the organic insulator[25].
A polymer electrolyte membrane for battery application must play the following roles: must enable positive ion transport such as Li+ between the electrodes, must block the electron transport, and must be rigid to prevent direct contact between the electrodes[26]. The application of PMMA in the polymer electrolyte was due to the amorphous nature for porosity’s sake and the mechanical strength it has for the provision of the rigidity to the polymer electrolyte membrane.
Sensor application
In search of the production of a quasi-solid-state dye-sensitized solar cell (DSSC) using a high conductivity polymer gel electrolyte, a suitable polymeric material was needed to be a host matrix in the composite. Therefore, PMMA was found to be a good and compatible polymer for this purpose. This was attributed to its mechanical strength, compatibility, and optical clarity[27].
Solar and nanotechnology applications
Due to the wider application of nanocomposites in the field of nanotechnology, many researchers focused their attention on nanocomposites, their fabrication, and applications. Perween et al. reported the use of PMMA and graphite to fabricate plastic chip electrodes (PCEs) via a simple solution casting method. This characterization was made using microscopy (SEM and AFM) as well as thermal properties (TGA), and mechanical and electrical properties. The fabricated electrode was economically inexpensive, multipurpose, and dispensable for various applications[28].
- Malcom, P.S. Polymer Chemistry: An Introduction. 3rd ed.; Oxford University Press: NY, pp 167–176, 256–276.
- Henri, L. Thermohygroelastic Properties of Polymethylmethacrylate; 2007, Netherlands. pp. 11–13.
- Demir, M. M.; Memesa, M.; Castignolles, P.; Wegner, G. Macromolecular Rapid Communications. 2006, 27 (10), 763–770.
- Hashim, H.; Adam, N. I.; Zaki, N.H.M.; Mahmud, Z.S.; Said, C.M.S.; Yahya, M.Z.A.; Ali, A.M.M. Conference on Science and Social Research 2010 (CSSR 2010), Kuala Lumpur, Malaysia, 485–488.
- Henry, A.C.; Tutt, T.J.; Galloway, M.; Davidson, Y.Y.; McWhorter, C.S.; Soper, S.A.; McCarley, R.L. Analytical Chemistry 2000, 72(21), 5331–5337.
- Lee, L.H.; Chen, W.C. Chem. Mater. 2001, 15, 1137–1142.
- Shah, J. J.; Geist, J.; Locascio, L. E.; Gaitan, M.; Rao, M. V.; Vreeland, W. N. “Surface modification of poly(methyl methacrylate) for improved adsorption of wall coating polymers for microchip electrophoresis”, Electrophoresis 2006, 27(19), 3788–3796.
- Adhikari, B.; Majumdar, S. “Polymers in sensor applications”, Progress in Polymer Science 2004, 29(7), 699–766.
- Isha, A.; Yusof, N.A.; Ahmad, M.; Suhendra, D.; Yunus, W.M.Z.W.; Zainal, Z. Sensors and Actuators B: Chemical. 2006, 114(1), 344–349.
- Kost, J.; Langer, R. “Responsive polymeric delivery systems”, Advanced Drug Delivery Reviews. 2012, 64, 327–341.
- Beruto, D.T.; Botter, R.; Fini, M. Biomaterials. 2002, 23(12), 2509–2517.
- Shi, M.; Kretlow, J.D.; Spicer, P.P.; Tabata, Y.; Demian, N.; Wong, M.E.; Kasper, F.K.; Mikos, A.G. Journal of Controlled Release 2011, 152(1), 196–205.
- Mishra, S.; Sen, G. International Journal of Biological Macromolecules. 2011, 48(4), 688–694.
- Wang, M.; Pramoda, K.P.; Hong, S. Polymer 2005, 46, 11510–11516.
- George, O. Principles of Polymerization, 4th ed.; Wiley: NJ, 2004, pp 198–235.
- Wang, J.-S.; Matyjaszewski, K. Journal of the American Chemical Society. 1995, 117(20), 5614–5615.
- Grimaud, T.; Matyjaszewski, K. Macromolecules. 1997, 30(7), 2216–2218.
- Charles, A.H.; Edward, M.P. Plastics Materials and Processes, in Concise Encyclopedia; Wiley: NJ, 2003, pp. 42–44.
- Van Krevelen, D.W.; Nijenhuis, K. T. Properties of Polymers; Elsevier: Amsterdam, 2000, pp. 106, 322.
- Charles, A.H. Handbook of Plastics Processes; Wiley: NJ, 2006, pp. 1–7.
- Ishitake, K.; Satoh, K.; Kamigaito, M.; Okamoto, Y. Polymer Chemistry. 2012, 3(7), 1750–1757.
- Zuhair, J.; Abdul Amer, J.K.A.; Sura Fahim, A. “Chitosan/PMMA bioblend for drugs release applications”, International Journal of Engineering and Technology 2014, 4(5), 318–324.
- Tai, Y.; Wang, L.; Gao, J.; Amer, W.A.; Ding, W.; Yu, H. Journal of Colloid and Interface Science. 2011, 360(2), 731–738.
- Camara, R.M.; Portela, R.; Gutierrez-Martin, F.; Sanchez B. Global NEST Journal 2014, 6(3), 525–535.
- Haik, M.Y.; Ayesh, A.I.; Abdulrehman, T.; Haik, Y. Materials Letters. 2014, 124(0): 67–72.
- Hallinan, D.T.; Balsara, N.P. Polymer Electrolytes, in Annual Review of Materials Research, Vol 43, D.R. Clarke, Ed.; 2013, pp. 503–525
- Shen, J.; Li, Z.; Cheng, R.; Luo, Q.; Luo, Y.; Chen, Y.; Chen, X.; Sun, Z.; Huang, S. ACS Applied Materials & Interfaces 2014, 6(20), 17454–17462.
- Perween, M.; Parmar, D.B.; Bhadu, G.R.; Srivastava, D.N. “Polymer-graphite composite: a versatile use and throw plastic chip electrode”, Analyst 2014, 139(22), 5919–5926.
Methyl methacrylate is one of the most common
methacrylates. This acrylic monomer, the essential
component of the fluid mixed to the powder, may
cause allergic contact dermatitis mainly in dental
technicians and dentists. Cases were also reported in
those using seulptured nails and in ceramics workers.
Poly(methyl methacrylate) is a hard, rigid transparent substance. Straight poly(methyl methacrylate) is somewhat tougher than polystyrene but is less tough than the ABS polymers. An outstanding property of
poly(methyl methacrylate) is its clarity. The material absorbs very little
visible light but there is about 4% reflection at each polymer-air interface for
normal incident light. Thus the transmission of normal incident light through
a sheet of the polymer is about 92%. Poly(methyl methacrylate) is a polar
material and has a rather high dielectric constant and power factor; it is a
good electrical insulator at low frequencies but is less satisfactory at high
frequencies.
Poly(methyl methacrylate) prepared by free radical polymerization is amorphous and is therefore soluble in solvents of similar solubility parameter. Effective solvents include aromatic hydrocarbons such as benzene and toluene; chlorinated hydrocarbons such as chloroform and ethylene dichloride; and esters such as ethyl acetate and amyl acetate. Some organic materials, although not solvents for the polymer, cause crazing and cracking, e.g. aliphatic alcohols and amines. Poly(methyl methacrylate) has very good resistance to attack by water, alkalis, aqueous inorganic salts and most dilute acids. Some dilute acids such as hydrocyanic and hydrofluoric acids, however, do attack the polymer, as do concentrated oxidizing acids. Poly(methyl methacrylate) has much better resistance to hydrolysis than poly(methyl acrylate), probably by virtue of the shielding presented by the a-methyl group. Poly(methyl methacrylate) may be converted to poly(sodium methacrylate) only by rather drastic treatment with, for example, molten sodium hydroxide.
A further outstanding property of poly(methyl methacrylate) is its good outdoor weathering, in which respect the material is markedly superior to most other thermoplastics. After several years under tropical conditions the colour change is extremely small. When poly(methyl methacrylate) is heated above the glass transition temperature (105°C) it becomes rubbery and sheet material is easily manipulated at 150-160°C. Above about 200°C decomposition becomes appreciable and at 350-450°C a nearly quantitative yield of monomer is readily obtained. Thus the recovery of monomer from scrap polymer is a feasible proposition.
Poly(methyl methacrylate) prepared by free radical polymerization is amorphous and is therefore soluble in solvents of similar solubility parameter. Effective solvents include aromatic hydrocarbons such as benzene and toluene; chlorinated hydrocarbons such as chloroform and ethylene dichloride; and esters such as ethyl acetate and amyl acetate. Some organic materials, although not solvents for the polymer, cause crazing and cracking, e.g. aliphatic alcohols and amines. Poly(methyl methacrylate) has very good resistance to attack by water, alkalis, aqueous inorganic salts and most dilute acids. Some dilute acids such as hydrocyanic and hydrofluoric acids, however, do attack the polymer, as do concentrated oxidizing acids. Poly(methyl methacrylate) has much better resistance to hydrolysis than poly(methyl acrylate), probably by virtue of the shielding presented by the a-methyl group. Poly(methyl methacrylate) may be converted to poly(sodium methacrylate) only by rather drastic treatment with, for example, molten sodium hydroxide.
A further outstanding property of poly(methyl methacrylate) is its good outdoor weathering, in which respect the material is markedly superior to most other thermoplastics. After several years under tropical conditions the colour change is extremely small. When poly(methyl methacrylate) is heated above the glass transition temperature (105°C) it becomes rubbery and sheet material is easily manipulated at 150-160°C. Above about 200°C decomposition becomes appreciable and at 350-450°C a nearly quantitative yield of monomer is readily obtained. Thus the recovery of monomer from scrap polymer is a feasible proposition.
PMMA/HA (Hydroxyapatite) composites have be used in biomedical applications such as dentistry, orthopedic retainers, and bone replacement. It has been used as substrate for graphene growth.
Some studies report its use as
PMMA-titania hybrid optical thins films
PMMA/polystryrene/clay nanocomposites
PMMA/polyurethane/carbon black nanocomposites for methanol fuel cells.
Some studies report its use as
PMMA-titania hybrid optical thins films
PMMA/polystryrene/clay nanocomposites
PMMA/polyurethane/carbon black nanocomposites for methanol fuel cells.
Poly(methyl methacrylate) may be used as a reference suspension polymer for the analysis of the composition of poly(methyl methacrylate) (PMMA) by gas chromatography method.
Poly(methyl methacrylate) is used in production of Carbonate-olefin based copolymer for molded plastics.
The polymerization of methyl methacrylate:
is readily accomplished by bulk, solution, suspension and emulsion techniques. Of these methods, bulk and suspension polymerization are mainly used for the production of the homopolymer.
(a) Bulk polymerization
Techniques which involve a combination of bulk polymerization and casting are extensively used in the manufacture of poly(methyl methacrylate) sheet. In most processes, the first step is the preparation of a partially polymerized material. Typically, monomer is stirred with benzoyl peroxide (0.5%) at 90??C for about 10 minutes to give a syrup which is then cooled to room temperature. Colourant, plasticizer and ultraviolet absorber, if required, are added at this point. At this stage the degree of conversion of monomer to polymer is about 20%; the use of such a syrup reduces shrinkage in the casting cell and also lessens leakage from the cell. The syrup is then poured into a casting cell, consisting of two glass plates separated by a rubber gasket. The plates are held together by spring-loaded clamps so that the plates continuously move together in response to the shrinkage of approximately 20% which occurs on conversion of monomer to polymer. The filled cell is then passed through a heating tunnel wherein the temperature is maintained at 40??C for 15 hours and then 95??C for 1 hour. The sheet is then cooled and removed from the cell. With castings of thickness greater than about 2 cm, the exothermic reaction may result in local temperatures above the boiling point of the monomer (100Se) and bubbles may form. In such cases, polymerization may be carried out under pressure so that the boiling point of the monomer is raised.
Rod is also manufactured by casting. In one process, syrup is contained in vertical aluminium tubes which are very slowly lowered into a bath at 40??C. As the lowest portion of syrup polymerizes it contracts and the syrup above moves downwards. In this way a homogeneous rod, free from voids, is obtained. Dentures are normally made from a polymer-monomer dough in a plaster mould. Bulk polymerization carried out in the preparation of sheet, as described above, results in polymer of very high average molecular weight (??106).
(b) Suspension polymerizution
Suspension polymerization of methyl methacrylate is used mainly for the production of injection moulding and extrusion grades of polymer. Suspension polymer is also used in the preparation of polymer-monomer doughs for dentures. Polymerization is carried out batch-wise in a stirred reactor, jacketed for heating and cooling; the reactor is capable of withstanding a pressure of 0.3--0.4 MPa (3-4 atmospheres).
Reaction is carried out under nitrogen. Typically, the mixture is initially heated to about 80??C but the exothermic reaction causes the temperature to rise to about 120??C, with accompanying increase in pressure. Polymerization is rapid and is complete in about 1 hour. The suspension is cooled and acidified with sulphuric acid to remove the suspending agent. The beads of polymer are then filtered off, washed and dried in air at about 80??C. The dried beads may be used for moulding without further treatment or they may be compounded with additives (e.g. colourants), extruded and granulated.
Suspension polymerized poly(methyl methacrylate) normally has an average molecular weight of about 60000.
is readily accomplished by bulk, solution, suspension and emulsion techniques. Of these methods, bulk and suspension polymerization are mainly used for the production of the homopolymer.
(a) Bulk polymerization
Techniques which involve a combination of bulk polymerization and casting are extensively used in the manufacture of poly(methyl methacrylate) sheet. In most processes, the first step is the preparation of a partially polymerized material. Typically, monomer is stirred with benzoyl peroxide (0.5%) at 90??C for about 10 minutes to give a syrup which is then cooled to room temperature. Colourant, plasticizer and ultraviolet absorber, if required, are added at this point. At this stage the degree of conversion of monomer to polymer is about 20%; the use of such a syrup reduces shrinkage in the casting cell and also lessens leakage from the cell. The syrup is then poured into a casting cell, consisting of two glass plates separated by a rubber gasket. The plates are held together by spring-loaded clamps so that the plates continuously move together in response to the shrinkage of approximately 20% which occurs on conversion of monomer to polymer. The filled cell is then passed through a heating tunnel wherein the temperature is maintained at 40??C for 15 hours and then 95??C for 1 hour. The sheet is then cooled and removed from the cell. With castings of thickness greater than about 2 cm, the exothermic reaction may result in local temperatures above the boiling point of the monomer (100Se) and bubbles may form. In such cases, polymerization may be carried out under pressure so that the boiling point of the monomer is raised.
Rod is also manufactured by casting. In one process, syrup is contained in vertical aluminium tubes which are very slowly lowered into a bath at 40??C. As the lowest portion of syrup polymerizes it contracts and the syrup above moves downwards. In this way a homogeneous rod, free from voids, is obtained. Dentures are normally made from a polymer-monomer dough in a plaster mould. Bulk polymerization carried out in the preparation of sheet, as described above, results in polymer of very high average molecular weight (??106).
(b) Suspension polymerizution
Suspension polymerization of methyl methacrylate is used mainly for the production of injection moulding and extrusion grades of polymer. Suspension polymer is also used in the preparation of polymer-monomer doughs for dentures. Polymerization is carried out batch-wise in a stirred reactor, jacketed for heating and cooling; the reactor is capable of withstanding a pressure of 0.3--0.4 MPa (3-4 atmospheres).
Reaction is carried out under nitrogen. Typically, the mixture is initially heated to about 80??C but the exothermic reaction causes the temperature to rise to about 120??C, with accompanying increase in pressure. Polymerization is rapid and is complete in about 1 hour. The suspension is cooled and acidified with sulphuric acid to remove the suspending agent. The beads of polymer are then filtered off, washed and dried in air at about 80??C. The dried beads may be used for moulding without further treatment or they may be compounded with additives (e.g. colourants), extruded and granulated.
Suspension polymerized poly(methyl methacrylate) normally has an average molecular weight of about 60000.
Poly (methyl methacrylate) (PMMA) is an amorphous transparent thermoplastic polymer. PMMA is recognized as an optical polymer based on its refractive index of 1.49. Hence, it is used in optical fibers.It finds uses in biological applications because of its low water absorption capability and biocompatible.The maximum moisture content of PMMA is 1.71% and SBF absorption is 1.96%.Simulated Body fluid test (SBF) is a method to characterize the in vitro bioactivity of ceramic materials, by immersing the materials in an aqueous SBF solution.
Questionable
carcinogen with experimental tumorigenic
data by implant route. When heated to
decomposition it emits acrid smoke and
irritating fumes. Used as the main
constituent of acrylic sheet, moldmg, and
extrusion powders.
Preparation Products And Raw materials
Raw materials
Related articles
Related Product Information
PROMPT×
PROMPT
The What'sApp is temporarily not supported in mainland China
The What'sApp is temporarily not supported in mainland China
Cancel
Determine