Zirconia (Zirconium dioxide): General properties; Commercial zirconia grades and Preparation
General properties
Pure zirconium dioxide (ZrO2), also called zirconia, is a dense material (5850 kg.m–3) that exhibits a high temperature of fusion (2710°C) and a good thermal conductivity (1.8 Wm–1K–1). Electrically speaking, zirconia is a dielectric at room temperature but becomes a good ionic conductor at high temperatures. Actually, cubic zirconia is a solid ionic electrolyte that allows oxygen anions to migrate through the crystal structure under an electric field at temperatures above 800°C.
Optically, zirconia has a high index of refraction, which allows it to be used for increasing the refractive index of some optical glasses. Chemically, zirconia exhibits an excellent chemical inertness and corrosion resistance to many strong mineral acids, liquid metals, and molten salts up to high temperatures well above the melting point of alumina. Zirconia is not wetted by many metals and is therefore an excellent crucible material when corrosive melts (e.g., molten alumina and titanium slag) are absent.
It can be used continuously or intermittently at temperatures up to 2200°C in neutral or oxidizing atmospheres. However, above 1600°C, zirconia reacts with alumina, and above 1650°C, in contact with carbon, zirconia forms zirconium carbide (ZrC). It has been used successfully for melting alloy steels and the noble metals. Nevertheless, zirconia in its chemically pure state exhibits poor mechanical and thermal properties that are inappropriate for use in structural and advanced ceramics.
Actually, the polymorphism of pure zirconia exhibits deleterious phase transitions between room temperature and its melting point. These phase changes, accompanied by important relative volume changes, create a dense population of microcracks for the sake of toughness and thermal shock resistance. Polymorphs of zirconia (ZrO2) are shown below:
However, to prevent the first disastrous phase transition, it is possible to stabilize hightemperature cubic zirconia introducing foreign bivalent, trivalent, and/or tetravalent cations
into its structure. Once stabilized, zirconia is stable from room temperature up to its melting
point without any phase changes, and its thermal expansion varies linearly with temperature. The doped material demonstrates superior mechanical, thermal, and electrical properties owing to the modification of its crystal structure.
Commercial zirconia grades and Preparation
Unstabilized zirconia
Pure zirconia is an important constituent of ceramic colors and an important component of lead-zirconia-titanate electronic ceramics. Pure zirconia can be used as an additive to enhance the properties of other oxide refractories. It is particularly advantageous when added to high-fired magnesia and alumina bodies. It promotes sinterability and, with alumina, contributes to abrasive characteristics.
Zirconia is usually produced from zircon flour. Therefore, to produce zirconia from zircon, the first step is to convert zircon to zirconyl chloride dihydrate. The process starts with the preparation of disodium metazirconate (Na2ZrO3) by digesting zircon into molten sodium hydroxide as follows: ZrSiO4(s) + NaOH(l) —> Na2ZrO3(s). Then the sodium zirconate is dissovled in concentrated hydrochloric acid: Na2ZrO3(s) + 2HCl(l) —> ZrOCl2 · 8H2O(s).
There are two methods used to make zirconia from zirconyl chloride dihydrate (ZrOCl2.8H2O): thermal decomposition and precipitation. In the thermal decomposition method, upon heating above 200°C, zirconyl chloride dihydrate loses its hydratation water. Afterwards, at a higher temperature anhydrous ZrOCl2 decomposes during calcination into chlorine gas and yields zirconia:
ZrOCl2 · 8H2 O(s) —> ZrOCl2 (s) + 8H2 O(g); ZrOCl2(s) + 1/2O2(g) —> ZrO2(s) + Cl2(g).
In the precipitation method, zircornyl chloride dihydrate is dissolved into water, and after addition of aqueous ammonia a precipitate of zirconium hydroxide is obtained. The precipitate of zirconium hydroxide (Zr(OH)4) is washed in order to obtain a chlorinefree product. The solid is recovered by filtration to yield a wet powder that after calcination and quenching into liquid nitrogen yield a high-quality zirconia powder.
Partially stabilized zirconia
Partially stabilized zirconia (PSZ) is a mixture of various zirconia polymorphs, because insufficient cubic-phase-forming oxide has been added and a cubic plus metastable tetragonal ZrO2 mixture is obtained. PSZ is a transformation-toughened material. Microcracks and induced stress may be two explanations for the toughening in partially stabilized zirconia. PSZ has been used where extremely high temperatures are required. PSZ is also used experimentally as heat engine components, such as cylinder liners, piston caps, and valve seats.
Fully stabilized zirconia
Fully stabilized zirconia, also called cubic stabilized zirconia (CSZ), is essentially a single-phase cubic material with large grain sizes of 10 ~ 150 μm that result when the stabilizer content and sintering temperature place it entirely in the cubic-phase region. Fully yttria-stabilized zirconia (YSZ) is an excellent oxygen anion conductor that has been used extensively either as oxygen sensor or anion exchange membrane in solid oxide fuel cells (SOFCs). Other applications include grinding media and advanced ceramics due to its hardness and high thermal shock resistance.
In order to achieve the requirement of the presence of cubic and tetragonal phases in the microstructure of zirconia, stabilizers, i.e., magnesia, calcia, or yttria must be introduced into pure zirconia powders prior to sintering. Stabilized zirconia can be formed during a process called in situ stabilizing. Before the forming processes, such as molding, pressing, or casting, a blend of fine particles of stabilizer and monoclinic zirconia is prepared. Then the mixture is used for forming of green body. The phase conversion is accomplished by sintering the doped zirconia at 1700°C. During the firing (sintering), the phase conversion takes place. On the other hand, high-quality stabilized zirconia powder is made by a coprecipitation process. Stabilizers are then introduced before precipitation of zirconium hydroxide.
Preparation of zirconia by alkaline leaching
Zircon is roasted with sodium hydroxide and calcia at 600 to 1000°C. During the process silica reacts with calcium and sodium to yield calcium and sodium metasilicates. After acid leaching, the product is dyed and calcined to yield pure zirconia with less than 0.10 wt.% residual silica.
You may like
Related articles And Qustion
See also
Lastest Price from Zirconium dioxide manufacturers

US $0.00-0.00/kg2025-05-23
- CAS:
- 1314-23-4
- Min. Order:
- 1kg
- Purity:
- 99.7%min
- Supply Ability:
- 20mt
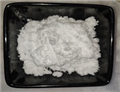
US $1.00/PCS2025-04-21
- CAS:
- 1314-23-4
- Min. Order:
- 1PCS
- Purity:
- 99%
- Supply Ability:
- 100mt