What is the biosynthetic route of Benzyl acetate?
Benzyl acetate is an aromatic ester with a scent similar to jasmine, gardenia, and lily of the valley. It is often used as a base flavoring ingredient in perfumes, cosmetics, and soap flavors. It is also one of the largest varieties in the synthetic flavoring industry.
Benzyl acetate occurs naturally in plants such as cloves, chamomile, jasmine, and hyacinth; however, extracts obtained from these plants are not sufficient to meet global usage (about 10,000 tons per year). Therefore, benzyl acetate is mainly produced by chemical synthesis. In the chemical synthesis method, Benzyl acetate is mainly obtained by the esterification reaction of acetic acid and benzyl alcohol (BALC). However, this method is usually carried out in the presence of H2SO4 and has the disadvantages of non-renewable raw materials, excessive side reactions, and serious environmental pollution. Therefore, in order to adopt a more sustainable method, the precursor BALC was synthesized from glucose through system engineering of Escherichia coli, and then Benzyl acetate was synthesized by lipase. The specific reaction steps are as follows:
Starting from phenylpyruvate, which is the direct precursor of phenylalanine (L-Phe). The pathway consists of three enzymes, hydroxyglycolate synthase (HmaS) from Amycolatopsis orientalis, glycolate dehydrogenase (MdlB) from Pseudomonas putida, and phenylglyoxylate decarboxylase (MdlC). These three enzymes sequentially convert phenylpyruvate to benzaldehyde (BALD) via glycolate and phenylglyoxylate. Multiple endogenous alcohol dehydrogenases (ADH) and aldehyde-keto reductases (AKR) in Escherichia coli convert BALD to BALC. This pathway involves two decarboxylation reactions and is therefore less carbon efficient. The CoA-dependent β-oxidation pathway releases acetyl-CoA from the common precursor L-Phe to provide energy for the TCA cycle or substrate for the synthesis of acetylated products, which is a more carbon efficient process. In this pathway, phenylalanine ammonia lyase converts L-Phe to cinnamic acid (CA) and cinnamate: CoA ligase catalyzes the conversion of CA to cinnamoyl-CoA (CA-CoA). Enoyl-CoA hydratase, 3-hydroxyacyl-CoA dehydrogenase, and 3-oxoacyl-CoA ketohydrolase sequentially convert CA-CoA to BA via 3-hydroxyphenylpropionyl-CoA (HPP-CoA) and 3-ketophenylpropionyl-CoA (KPP-CoA) (Figure 1, route I). In principle, BA produced by this pathway can be converted to BALD when carboxylic acid reductase (CAR) is co-expressed (Figure 1, route I). Endogenous ADH and AKR in E. coli can then spontaneously convert BALD to BALC. In plants, BALD is a natural product. Different from the above pathway, in plants, 3-ketoacyl-CoA thiolase (KAT) converts KPP-CoA in the β-oxidation pathway to benzoyl-CoA (BA-CoA), and then benzaldehyde synthase (BS) reduces BACoA to BALD (Figure 1, route II). Finally, Benzyl acetate was synthesized by biocatalytic method using lipase in the presence of BALC. For example, by expressing thermostable chloramphenicol acetyltransferase from Staphylococcus aureus (CATSa) in E. coli, about 150 mg/L of benzyl acetate could be produced with 2 g/L BALC. When engineered E. coli carrying alcohol acyltransferase (ATF1) from Saccharomyces cerevisiae was supplemented with 2.0 g/L BALC, 1177.98±45.72 mg/L of benzyl acetate could be produced.
References:
[1] QIN KE. Metabolic engineering of Escherichia coli for high-level production of benzyl acetate from glucose.[J]. Microbial Cell Factories, 2024, 23 1. DOI:10.1186/s12934-024-02513-y.You may like
Related articles And Qustion
Lastest Price from Benzyl acetate manufacturers
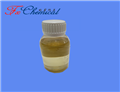
US $0.00/KG2025-04-21
- CAS:
- 140-11-4
- Min. Order:
- 1KG
- Purity:
- 99.0%
- Supply Ability:
- 1000KG/month

US $10.00/kg2025-04-21
- CAS:
- 140-11-4
- Min. Order:
- 1kg
- Purity:
- 99%
- Supply Ability:
- 100 mt