Vinyl acetate: Properties, Production process and Uses
Vinyl acetate, also known as acetic acid vinyl ester, ethenyl acetate, ethenyl ethanoate, vinyl acetate monomer and acetoxyethene, is a derivative of acetylene and acetic acid. Molecular formula: C4H6O2, molecular weight: 86.0892. The chemical structure is:
Properties of vinyl acetate
Vinyl acetate is a colorless, transparent and flammable liquid with a strong odor. It is soluble in most organic solvents and slightly soluble in water. The physical properties of vinyl acetate are listed in Table 6.1.
Vinyl acetate is anesthetic and irritating, causing inflammation of the mouth and red spots on the eyes in the air with high concentrations of its vapor. The toxicity of this product is low, and the oral LD50 of rats is 2,920 mg.kg–1.
Process for manufacture of vinyl acetate
The industrial processes for production of vinyl acetate include acetylene route and ethylene route. Currently, ethylene route accounts for more than 70% of the total production capacity of vinyl acetate in the world. However, in areas with abundant coal and natural gas resources, the acetylene route to vinyl acetate is quite competitive. In China, due to the abundant coal resources and relatively insufficient petroleum resources, acetylene route dominates the production of vinyl acetate, accounting for about 80% of the total production capacity.
Acetylene route
Acetylene undergoes an addition reaction with acetic acid vapor in the presence of a zinc acetate catalyst supported on activated carbon to produce vinyl acetate. The reaction is carried out at a temperature of 170–230°C under a pressure of 35–40 kPa. The reaction equation is as follows:
The process flow diagram of vinyl acetate production is shown in Figure 6.1. Acetic acid is continuously fed to an acetic acid evaporator where it is contacted with purified fresh anhydrous acetylene and recycled acetylene. The operating temperature and pressure of the evaporator are 70–80°C and 27–34 kPa, respectively. The mixture of acetic acid vapor and acetylene (molar ratio 1:4–5) is heat exchanged with the hot gas from the reactor, and subsequently heated to 170–195°C by steam, and then introduced into the vinyl acetate synthesis reactor filled with zinc acetate catalyst supported on activated carbon. In the reactor, acetylene reacts with acetic acid to form vinyl acetate. The outlet gas mixture from the reactor, which mainly contains vinyl acetate, unreacted acetic acid, acetylene and by-products, is partially condensed by heat exchange with the feed mixture, and further condensed by a condenser. Then, the resultant condensate is introduced into a gas–liquid separator for phase separation. The gas phase from the top of the gas–liquid separator is sent to a washing tower to remove and recover the small amount of acetic acid and vinyl acetate in it by washing with recycled acetic acid, and then recycled to the evaporator by a compressor. The liquid phase from the bottom of the gas–liquid separator and the liquid from the bottom of the washing tower are sent to the light fraction removal tower to remove the light component (acetaldehyde). The bottom product of the light fraction removal tower is introduced into the vinyl acetate fractional distillation tower. Vinyl acetate with a purity of 99.9% is obtained from the top product of the tower. The bottom product of the vinyl acetate fractional distillation tower is sent to acetic acid purification tower to remove crotonaldehyde from the top of the tower. The bottom product of the acetic acid purification tower is introduced into the heavy fraction removal tower to remove the heavy component, and the acetic acid with a purity of more than 99% is obtained at the top of the tower, which is recycled to the washing tower and the evaporator.
In order to avoid the polymerization of vinyl acetate, hydroquinone was added as a polymerization inhibitor to the feeds of the light fraction removal tower and the vinyl acetate fractional distillation tower.
The main by-products are acetaldehyde and crotonaldehyde. The conversion of acetylene per pass is in the range from 60% to 75%, the selectivity to vinyl acetate is 99% based on acetic acid, and 93% based on acetylene.
Ethylene route
Ethylene reacts with oxygen and acetic acid in the presence of Pd–Au (or Pt) catalyst
at a temperature of 100–200°C under a pressure of 0.6–0.8 MPa, and the resultant
reaction mixture is subjected to separation for vinyl acetate product.
The ethylene route can be performed in liquid phase or in gas phase. However, the catalyst system used in liquid phase contains chloride ions, which is highly corrosive to equipment, resulting in a short operation time. Therefore, liquid phase process has been eliminated.
The traditional ethylene route mainly includes Bayer process and USI process, both of
which adopt a gas phase fixed-bed process, and the technical processes are also similar.
The difference between them is that the catalyst used in Bayer process is Pd–Pt supported
on silica gel, while the catalyst used in USI process is Pd–Au supported on α-Al2O3. Bayer
process is more popular in industrial production because of higher conversion per pass of
acetic acid and better selectivity to vinyl acetate than those of USI process.
Uses of vinyl acetate
Vinyl acetate is mainly used for production of polyvinyl acetate (PVAc), polyvinyl
alcohol (PVA), ethylene–vinyl acetate (VAE) copolymer, vinyl chloride–vinyl acetate
copolymer and other derivatives. These derivatives are used in chemical products
such as coatings, adhesives, vinylon, films and vinyl copolymer resins.
You may like
Related articles And Qustion
See also
Lastest Price from Vinyl acetate manufacturers
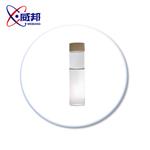
US $1.00/KG2025-04-21
- CAS:
- 108-05-4
- Min. Order:
- 1KG
- Purity:
- 99%
- Supply Ability:
- 10 mt

US $0.00-0.00/Kg2025-04-21
- CAS:
- 108-05-4
- Min. Order:
- 1Kg
- Purity:
- 99.99%
- Supply Ability:
- 20 tons