A thoroughly ground mixture of 3.6 g. of dry V2O5 and 9.4 g. of VCl3 is placed at the closed end of a l-m.-longtube, and 0.9 ml. of VOCl3 is then added. The upper part of the tube must be free of traces of these substances. The tube, filled with air, is melt-sealed, and is covered along its entire length with a sheet-metal jacket; its lower third, in a slightly inclined position, is then heated to about 600℃ with a tubular electric furnace. The sheet-metal jacket provides a temperature gradient along which the product VOCl2 sublimes out of the hot reaction zone. This procedure requires at least 4-5 days. However, the yield can be increased by longer heating time. Green needlelike crystals of VOCl2 are deposited in the cold part of the tube. The tube is opened at a suitable spot; the product is suspended in petroleum ether, ethyl ether or CCl4 to dissolve some adhering VOCl3, and then suction-filtered on a coarse fritted-glass filter. The relatively coarse filter separates the VOCl2 crystals from traces of finely divided hydrolysis products. The VOCl2 is freed of adhering solvent and stored under anhydrous conditions.
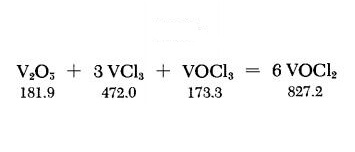