What are the synthesis methods of N-Vinyl-2-pyrrolidone?
Introduction
N-vinylated compounds are important fine chemicals because of their versatility for polymerization. In 1939, Walter Reppe, the pioneer in acetylene chemistry, first discovered the method of synthesizing N-Vinyl-2-pyrrolidone (NVP) and its polymer, i.e. polyvinylpyrrolidone, from acetylene[1]. NVP is commonly used as a reactive diluent for radiation curing in UV-coating, UV-inks, and UV adhesives. It is used as a monomer to produce water-soluble polyvinylpyrrolidone (PVP) used in pharmaceuticals, the oil field, cosmetics, food additives, and adhesives.
Synthesis method[2]
The synthesis routes of NVP mainly include vinylation of 2-pyrrolidone with acetylene, amination of γ-butyrolactone with ethanolamine, and vinyl exchange of 2-pyrrolidone with vinyl acetate or vinyl ether. The last process has not been applied in the industry because of high costs and complex problems of product separation from various by-products.
Production of NVP by vinylation of 2-pyrrolidone with acetylene
At present, all NVP manufacturers in the world produce NVP by vinylation of 2-pyrrolidone with acetylene. The production cost is the lowest for the production of NVP by vinylation of 2-pyrrolidone with acetylene, yet an acetylene generation and purification installation is required in the process. This process is the earliest and most mature method for the production of NVP, in which acetylene and 2-pyrrolidone are used as raw materials and KOH as a catalyst. The reaction mechanism is as follows:
It can be seen from the reaction mechanism that the reaction is divided into two stages. The first stage is the reaction of 2-pyrrolidone with KOH to form the potassium salt of 2-pyrrolidone, which is the catalyst for the subsequent two-step reactions. The KOH to be charged is generally from 1% to 3% by weight, and water is generated by preparing the potassium salt. Since the presence of water in the system causes the 2-pyrrolidone ring to break to form a by-product potassium 4-aminobutyrate, resulting in the deactivation of the catalyst, it is necessary to remove the water from the system. Usually, water is removed from the solution by vacuum distillation and nitrogen bubbling. It is required to make the water content less than 0.2%. The dehydration is generally carried out at a vacuum of 730–740 mmHg and a temperature from 80 to 130 °C.
In the second stage, acetylene is introduced, and the vinylation reaction is carried out at a pressure between 0.9 and 1.5 MPa and a temperature from 150 to 180 °C. In order to ensure the safety of acetylene under pressure, it is necessary to dilute acetylene with nitrogen; that is, compressors, reactors, and other equipment and pipelines are always running a mixture of acetylene and nitrogen instead of pure acetylene.
Production of NVP by amination of γ-butyrolactone with ethanolamine
Some manufacturers in China developed and adopted the production of NVP by amination of γ-butyrolactone with ethanolamine from 1995 to 2007. However, the cost of production is very high, even exceeding the market price of NVP with the reduction in the product's market price. Therefore, the process had been eliminated before 2007.
The reaction must be carried out at a higher temperature or in the presence of a catalyst. Certain cation exchange molecular sieves have desirable catalytic activity and selectivity for the reaction. The reaction requires an excess of ethanolamine, and the yield of NHP can reach over 90%. NHP undergoes a dehydration reaction to form NVP. The dehydration processes include direct and indirect dehydration. The direct dehydration of NHP is carried out at a temperature between 300 and 340 °C in the presence of a catalyst.
The direct dehydration of NHP is difficult, and the key is to prepare a catalyst with high activity and selectivity. The commonly used catalysts are oxides of aluminum, zirconium, tin, and silicon. The composite catalyst of zirconium oxide and tin oxide has both an acid center and a primary center, which has strong catalytic activity and high selectivity to NVP. At the reaction temperature of 300 to 340 °C, the single-pass conversion of NHP is above 70%, and the selectivity to NVP is over 90%. In the indirect dehydration process, NHP is converted into N-chloroethyl pyrrolidone by the reaction of NHP with a halogenating agent. Then, NVP is obtained by the removal of hydrogen chloride.
Commonly used halogenating agents are hydrogen chloride, thionyl chloride, and the like. The halogenation with thionyl chloride can be carried out at room temperature without a catalyst.
References
[1] Lifang Yan . “Synthesis of N-vinyl pyrrolidone by acetylene process in a microreactor.” Chemical Engineering Journal Advances 2 (2020): Article 100018.
[2] Li, Sifang. “Manufacture of Fine Chemicals from Acetylene.” 2021. 0.
You may like
Related articles And Qustion
See also
Lastest Price from N-Vinyl-2-pyrrolidone manufacturers
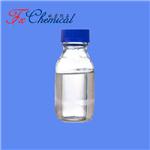
US $0.00/KG2025-04-21
- CAS:
- 88-12-0
- Min. Order:
- 200KG
- Purity:
- 98%min
- Supply Ability:
- 30tons/month
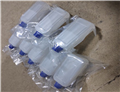
US $1.00/KG2025-04-21
- CAS:
- 88-12-0
- Min. Order:
- 1KG
- Purity:
- 99%
- Supply Ability:
- 10 mt