Tungsten carbide: General Properties; Industrial Preparation; Industrial Applications and Uses
Description and General Properties
Tungsten carbide, or hardmetal, was developed in the 1920s for wear-resistant dies to draw incandescent-lamp filament wire. Earlier efforts to manufacture the WC-W2 C eutectic alloy was unsuccessful because of its inherent brittleness; therefore researchers diverted their attention to powder metallurgy techniques. At present, these powder metallurgy techniques are being further developed and refined to reduce manufacturing costs and improve performance.
Tungsten carbide is in fact a composite material called cermet or hardmetal made of tungsten carbides in a metal matrix of cobalt. Tungsten carbide is harder than most steels, has greater mechanical strength, transfers heat quickly, and resists wear and abrasion better than other metals. Among the materials that resist severe wear, corrosion, impact, and abrasion, tungsten carbide is superior. Tungsten carbide is a dense (15,630 kg.m–3) and very hard ceramic material (1700–2400 HK). It exhibits outstanding mechanical properties with a Young's modulus of 668 GPa, a tensile strength of 344 MPa, and a compressive strength of 2683–2958 MPa. It has a high melting point of 2777°C and a thermal conductivity at 100°C of 86 W/mK.
Industrial Preparation
Most cemented carbides are manufactured by powder metallurgy, which consists in the preparation of the tungsten-carbide powder, powder consolidation, sintering, and postsintering forming. Tungsten-carbide powder is usually obtained by a carburization process and mixed with a relatively ductile matrix material such as cobalt, nickel, or iron and paraffin wax in either an attrition or ball mill to produce a composite powder. Spray drying yields uniform, spheroidized particles that are 100 to 200 mm in diameter. The powder is then consolidated into net and near-net-shape green compacts and billets by pressing and extrusion. Pressed billets can also be machined to shape before sintering. The density of the green compacts is around 45 to 65% of the theoretical. The green parts are then dewaxed at a temperature between 200 and 400°C and are then presintered between 600 and 900°C to impart adequate strength for handling. An alternative technology is a combination sinter-HIP process that combines dewaxing, presintering, vacuum sintering, and low-pressure HIP to speed up the overall cycle time.
Industrial Applications and Uses
Tungsten carbide can be used for a wide variety of applications. It has many applications that utilize its corrosion-resistant property such as wear plates, drawing dies, and wear parts for wire wearing machines. There are other applications that make use of its high hardness such as punches, bushings, dies, cylinders, discs, rings, and intricate shapes as well as performs and blanks. There are other minor applications such as in rusticator blades, sander nozzles, air jets, and sander guns. Tungsten carbide is also used primarily and extensively for making drill-tip tunneling, rock crushing, mining, and quarrying purposes, i.e., for most geological activities.
Tungsten carbide is also made into tiles for wear and abrasion resistance. It is also very useful in rebuilding worn parts. The application of tungsten carbide on industrial wearing surfaces has been proven to greatly enhance the performance factors for a whole spectrum of industrial applications. The service life of many kinds of machinery can be greatly prolonged by surface coating of wear-prone materials with tungsten carbide.
You may like
See also
Lastest Price from Tungsten carbide manufacturers
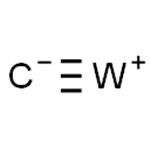
US $0.10/KG2024-08-05
- CAS:
- 12070-12-1
- Min. Order:
- 1KG
- Purity:
- 99.0%
- Supply Ability:
- 1000 tons

US $0.10/KG2024-08-05
- CAS:
- 12070-12-1
- Min. Order:
- 1KG
- Purity:
- 99.0%
- Supply Ability:
- 1000 tons