Synthesis of 1,6-Hexanediol Diacrylate
Introduction
1,6-hexanediol diacrylate (HDDA, Figure1) is an important bifunctional acrylate functional monomer in a series of acrylate products. HDDA is a monomer that can provide the best comprehensive properties such as softness, adhesion, activity and toughness in the existing bifunctional acrylates . It is widely used in ultraviolet (UV), external tough radiation (EB) or heat-curable coatings, inks, adhesives, casting plastics and other fields, and is also an excellent diluent [1-2].
At present, HDDA is mainly synthesized by direct esterification of 1,6-hexanediol (HDD) and acrylic acid (AA) in industry. P-toluenesulfonic acid or sulfuric acid is mainly used as catalyst [3]. The product is purified by alkali washing and water washing, which more alkaline waste liquid will be produced after treatment. It would cause serious corrosion to the equipment. In order to avoid the corrosion of the reactor, strong acidic cation resin is used to catalyze the synthesis of HDDA in recent years,which will encounter some shortcomings such as high catalyst cost and long esterification reaction cycle (4h) [4]. Secondly, the traditional method of synthesizing multi-functional acrylates mostly uses one or several mixtures of hydroquinone, phenothiazine, copper acetate, and p-hydroxyanisole as polymerization inhibitors [5]. These substances are highly toxic substances, and the waste liquid generated during the post-treatment water washing process which will do harm to the environment. In this work, 1,6-hexanediol diacrylate was synthesized using p-toluenesulfonic acid and phosphite as catalysts,while NaHSO4 /CuSO4 were chosen to be a composite polymerization inhibitor. The influencing factors of the esterification reaction were studied and the optimal reaction conditions were determined. The reaction system has a short reaction cycle. The crude product is easy to purify and the washing waste liquid has little environmental pollution.
Synthetic Principles of 1,6-hexanediol diacrylate(Scheme 1)
Synthesis method of 1,6-hexanediol diacrylate
A certain amount of HDD, AA, inhibitor, catalyst and water-carrying agent were added to a 500 mL four-necked flask equipped with a spherical condensing reflux tube, a water separator, a thermometer and a stirrer, respectively, and the esterification reaction was carried out at 80-90°C. The water-carrying agent no longer took out the water generated by the reaction, the temperature of the reaction liquid phase no longer rised,which showed that the esterification reaction is over. After the esterification reaction, the reaction liquid was cooled to room temperature, and then the water collected in the water separator and a certain volume of water-carrying agent were added to the reaction liquid to fully adjust the specific gravity of the reaction liquid. The product was washed with 5 % sodium bicarbonate and sodium hydroxide solution to neutralize the excess acid. The second step was washed with 20 % sodium chloride solution and distilled water to neutral, while the catalyst and inhibitor were removed at the same time. Finally, the solvent was removed under reduced pressure at 50°C, and the target product 1,6-hexanediol diacrylate (HDDA) was obtained.
Results and discussion
Factors affecting the esterification reaction [1]
(1)Acrylic acid/1,6-hexanediol
The direct esterification of HDD and AA to synthesize HDDA is a reversible reaction. If the HDD reaction is incomplete, it will not only cause the reaction to proceed in the negative direction, resulting in a decrease in yield, but also make it difficult to separate the target product diester, which may affect the purity of the product. In order to achieve complete HDD reaction and high yield, it is required that the reaction is carried out in the direction of generating 1,6-hexanediol diacrylate. Excessive AA is beneficial for the reaction to proceed in the positive direction. However, if the excess is too large, it will cause an increase in the acid value of the product, increase the load of water washing and purification in the later stage, and thus increase the cost. Therefore, it is necessary to choose a suitable ratio of acid to alcohol substances.
Firstly, the reaction conditions were set as follows : reaction temperature of 80-90℃, reaction time of 90 min, catalyst dosage of 1.5%, inhibitor dosage of 8.5% and water-carrying agent dosage of 65%.The effect of molar ratio of acid to alcohol on the yield of the product was investigated. It was found that the yield of 1,6-hexanediol diacrylate increased with the Initial increase of the molar ratio of AA/HDD. However, the yield of the product decreases with the further increase. When AA/HDD ratio was 2.5, the yield of 1,6-hexanediol diacrylate was the largest.
(2)Catalyst dosage
With the increase of the amount of catalyst, the yield of 1,6-hexanediol diacrylate (HDDA) increased continuously. When the amount of catalyst was more than 1.5%, the increase of the yield was not obvious. The main reason is that with the increase of the amount of catalyst, the number of molecules involved in the reaction increases, that is, the reaction rate accelerates, so that the yield increases. However, when the amount of catalyst reaches a certain value, and then increase the amount of catalyst, the number of molecules involved in the reaction does not increase significantly, so the yield increase is not obvious.
(3)Reaction time
With the extension of reaction time, the yield of 1,6-hexanediol diacrylate increased continuously. When the reaction time was more than 90 min, the yield of the product decreased slightly, which may be due to the polymerization of the product.Therefore, the optimal reaction time was 90 min.
(4)Reaction temperature
With the continuous increase of reaction temperature, the yield of 1,6-hexanediol diacrylate continues to increase; and when the reaction temperature exceeds 86℃, the increase in HDDA yield is not significant. Therefore, a reaction temperature range of 80-90℃ is more suitable.
(5)Water carrying agent dosage
This reaction selects cyclohexane as the water carrying agent (boiling point 80.7℃). In the experiment, the effect of changing the amount of cyclohexane as a water carrying agent on the yield of 1,6-hexanediol diacrylate was investigated. When the amount of cyclohexane exceeds 65%, the yield of the product does not change significantly. As the amount of water carrying agent increases, the concentration of the reaction system decreases, the reaction rate slows down, and the preparation period is extended. When the amount of cyclohexane is too small, the temperature of the reaction system increases, side reactions occur, the yield of the product decreases, and the color becomes darker.Therefore, the optimal amount of water carrying agent selected for this reaction is 65%.
(6)Selection of polymerization inhibitor
In this study, a binary compound inorganic inhibitor system (CuSO4 / NaHSO4) was screened, and it was found that the inhibitor system had a good inhibition effect. Under the same conditions, the effect of the amount of inhibitor on the yield of 1,6-hexanediol diacrylate was investigated. The results showed that when the amount of inhibitor was 8.5%, although the yield of 1,6-hexanediol diacrylate was slightly increased, the post-treatment time was prolonged, and the color of the product was deepened due to the addition of excessive inhibitor.
Conclusions
1.The optimum synthesis conditions were found to be as follows: acid-alcohol ratio 2.5; mass ratio of catalyst (catalyst: raw material)1.5%; mass ratio of inhibitor(inhibitor: acrylic acid) 8.5%; mass ratio of dehydrant (dehydrant: raw material) 65%; reaction time 90mins; reaction temperature 80-90℃. At the optimum reaction conditions, the synthesized 1,6-hexanediol diacrylate was colorless transparent liquid oil with high yield of 93.25%.
2.When CuSO4 / NaHSO4 is used as the polymerization inhibitor system, it not only overcomes the shortcomings of traditional polymerization inhibitors, but also has the characteristics of less dosage, easy removal after the completion of the reaction, non-sticking the reactor, and good color of the target product.
References
[1]Meng R, Li X.Synthesis of 1, 6-hexanediol diacrylate [J].Journal of Hunan University of Arts and Sciences:Natural Science Edition.2014,26(3):28-32.
[2]Lou Y.Synthesis of 1,6-hexanediol diacrylate [J].Petroleum technology and application, 2009,27(6):508-510.
[3]Zhang L.Preparation of 1,6-hexanediol diacrylate [P].China Patent, CN,200710151068.X,2009-6-24.
[4]Lou Y, Huang J, Du Y, et al. Synthesis of 1,6-hexanediol diacrylate catalyzed by strong acidic cationic resin [J].Petroleum technology and application,2010,28(6):492-494.
[5]Huang F, Wang J.Preparation of polyolacrylate [P].China Patent, CN,200510013311.2,2005-11-9.
You may like
Lastest Price from Hexamethylene diacrylate manufacturers
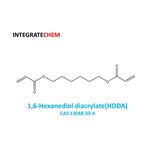
US $0.00/kg2025-08-26
- CAS:
- 13048-33-4
- Min. Order:
- 800kg
- Purity:
- 99%
- Supply Ability:
- 50 ton per month

US $0.00-0.00/kg2025-06-13
- CAS:
- 13048-33-4
- Min. Order:
- 1kg
- Purity:
- 99.0% min
- Supply Ability:
- 10tons