Industrial Preparation of Tantalum Metal
Tantalum can be prepared in several ways from different tantalum-containing materials. The primary source is columbotantalite ore, obtained after concentration of the raw ore by means of common ore-beneficiation processes (e.g., froth flotation, gravity separation). A secondary important source consists of the tin slag resulting from the smelting of niobium- tantalum-bearing cassiterite. The tin slag usually contains between 1.5 and 10 wt.% Ta2O5 and 1 to 3 wt.% Nb2O5. The tin slags are then leached by either an acid or alkaline solution, providing an insoluble Nb-Ta-bearing residue, made principally of niobium and tantalum pentoxides. Finally, a third recent source of niobium and tantalum comes from recycling of hardmetal containing tantalum and niobium carbides.
Industrial Preparation
Nevertheless, today the fractional crystallization of the fluoridated salt has been largely replaced in industry by solvent-extraction processes. Although early on several industrial processes were developed for the preparation of tantalum metal from tantalum compounds, including electrolysis in molten salts and the reduction of tantalum pentoxide with tantalum carbide, today the majority of tantalum metal is prepared by thermal reduction of potassium heptafluorotantalate with molten sodium.
Preparation of tantalum metal
Tantalum metal is obtained directly from the metallothermic reduction of potassium heptafluorotantalate with pure sodium metal. After reduction and cooling, the frozen mixture of both sodium fluoride and tantalum particles is crushed and the salt-encased tantalum powder recovered by a leaching operation with fresh water followed by acidified water. Tantalum particles are usually spherical in shape, with a tendency to form grapelike clusters during reduction. After drying and size selection by sieving, large tantalum particles are pressed, sintered, and electron-beam melted (i.e., EBmelted) in argon to give a bar and other mill products, while the fines with high specific surface area are used directly as capacitor anode powder.
Tantalum powder by the hydride-dehydride process
On the other hand, tantalum capacitor powder can also be prepared by the hydriding-dehydriding process, where the EB-ingot obtained previously is placed in an evacuated and purged furnace into which highly pure hydrogen is introduced. The tantalum is fully hydrided on slow cooling from 800°C under hydrogen. The brittle hydride is crushed, ground, and classified to yield powder with an average particle size of 5 μm. The final tantalum powder is obtained after dehydriding (i.e., reversible degassing) the tantalum-hydride powder.
You may like
Related articles And Qustion
Lastest Price from Tantalum manufacturers
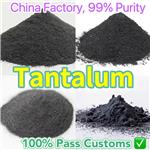
US $100.00-10.00/kg2025-04-21
- CAS:
- 7440-25-7
- Min. Order:
- 1kg
- Purity:
- 99% Purity (What/sapp: +86 18145728414)
- Supply Ability:
- 1000 Tons/Month
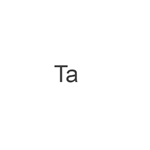
US $0.00/kg2022-09-27
- CAS:
- 7440-25-7
- Min. Order:
- 1kg
- Purity:
- 99%
- Supply Ability:
- 1000kg