Details of the processes used to produce vinylidene fluoride-hexafluoropropylene copolymers have not been disclosed but the copolymers may be prepared by emulsion polymerization under pressure using a persulphatebisulphite initiator system. Highly fluorinated surfactants, such as ammonium perfluorooctoate, are most commonly used in order to avoid chain
transfer reactions. The preferred vinylidene fluoride content for commercial
copolymers is about 70% mole. The structure of such a copolymer might be
represented as follows:

NMR studies confirm that head-to-tail arrangements predominate in the
copolymers. It may be noted that under the conditions normally used to
prepare commercial copolymers, hexafluoropropylene does not homopolymerize and so the molar proportion of this monomer in a copolymer cannot
exceed 50% whatever the composition of the monomer feed.
Commercial copolymers typically have an average molecular weight (Mn)
of about 70000.
Since the copolymers are saturated, they cannot be vulcanized by conventional sulphur systems. However, they may be vulcanized by aliphatic amines
and derivatives, aromatic dihydroxylic compounds and peroxides; all of these
methods are practised commercially. Free diamines react too quickly, causing premature vulcanization or scorching during mixing. One method of
reducing the tendency to scorch is to use diamines in the form of their inner
carbamates; hexamethylenediamine carbamate (VIII) and ethylenediamine
carbamate (IX) are employed commercially. Alternatively, the Schiff's bases
of diamines function as delayed-action vulcanizing agents; examples of
compounds of this type are N, N'-dicinnamylidene-l,6-hexanediamine (X)
and N, N'-disalicylpropylenediamine (XI).
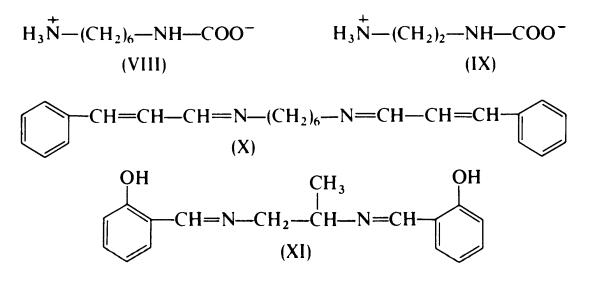