TECHNOLOGY FOR COMMERCIAL PRODUCTION OF TITANIUM SPONGE
Titanium sponge is the primary metal form of titanium. Titanium sponge is almost exclusively prepared by the Kroll process, with only one company in the world still using the Hunter process.58 The Kroll process dominates titanium-sponge production because other pyrometallurgical processes currently used to win a metal from its oxide are not suitable for preparing reactive metals like titanium. The two main reasons are, first, because the carbothermic reduction of titanium dioxide with carbon produces highly stable refractory titanium oxycarbides and, secondly, because the metallothermic reduction by molten alkali metals (e.g., Na) or alkaline-earth metals (e.g., Ca, Mg) does not remove completely the oxygen from the titanium-bearing oxide. Furthermore, at high temperatures, titanium is too reactive with nitrogen and oxygen, and to succeed the process must be conducted in a strictly inert atmosphere to prevent nitriding and oxidation. Both the Kroll and Hunter processes require the preparation of pure titanium tetrachloride, or simply “Ticle”。
DRDO has recently demonstrated state-of-the-art Combined Process Technology for the production of titanium-a material of strategic importance. With this, the country is now poised for commercial production of titanium the technology for which is currently available with a select group of developed countries.
Titanium—A Strategic Material
Titanium known for its excellent corrosion resistance, high strength and low density, is widely used for aero-engine and airframe structures in both civilian and military aircraft. Titanium-alloy components also find applications in satellite launch vehicles, rockets and missiles. Titanium is thus regARDEd as a metal of strategic importance. Excellent corrosion resistance of titanium to a wide range of chemicals, acids and alkalies has led to its use in thermal and nuclear power plants, desalination plants, fertilizer and petrochemical plants, and electroplating industries. Bio-medical implants, sports goods, automobiles, and architecture and consumer durables are some of the other emerging areas of titanium applications.
Production of Titanium Sponge
Titanium is extracted in the form of titanium sponge from its oxide minerals through magnesium reduction of its chloride intermeDIATe. However, the sponge production process is complex and cumbersome. It involves a number of complicated unit operations at high temperature and high levels of vacuum, involving a variety of corrosive media. The technical know-how for the production of titanium sponge has so far been available with a select group of developed countries comprising Japan, USA, Commonwealth of Industrial States, UK and China. As of now, India’s total titanium requirement is being met by imports even though it possesses a large reserve base of titanium minerals. Ilmenite (FeO.TiO2), an important titanium mineral, is widely distributed along the Indian coastal lines. With proven reserves exceeding 270 million tonnes, about 37 per cent of the total world Ilmenite reserves is located in the beach sands of the southern peninsular India.
Combined Process Technology
DRDO has been working on the development of an integrated flow sheet and technology for large scale production of titanium sponge starting from titanium tetrachloride which is produced by high temperature chlorination of oxide concentrates. Production of titanium sponge by Kroll process involving magnesium reduction of TiCl4 and vacuum separation of reduced mass for preparing sponge, free from entrapped Mg/MgCl2, has been one of the thrust areas of development at DRDO. Initially, DRDO demonstrated the technology for development of titanium sponge in 2000 kg batch size using the conventional two-step Kroll process involving separate equipment for ‘reduction’ and ‘vacuum distillation’. DRDO has recently demonstrated state-of-the-art Combined Process Technology, wherein reduction and vacuum separation processes are carried out in a single equipment thereby gaining benefits of energy and labour savings, improved productivity and also superior product quality. Further, this new technology has been demonstrated on a larger 4000 kg batch size to enable the establishment of a commercial plant without involving any further scale up.
Magnesium chloride is obtained as a by-product during the reduction of titanium tetrachloride by magnesium. It is customary in large industrial plants to recover magnesium and chlorine by fused-salt electrolysis and recycle them in the plant for achieving a reduced cost of production of titanium and thus an improved commercial viability. Fused-salt electrolysis is a complex technology especially for the production of magnesium. Realising the importance of the by-product recovery step for economic production of titanium, DRDO has fully developed the technology for the production of magnesium by fused-salt electrolysis in a state-of-the-art prototype multipolar cell capable of recovering 220 kg of Mg per day.
);You may like
Related articles And Qustion
See also
Lastest Price from Titanium manufacturers
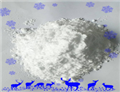
US $0.00/KG2024-03-16
- CAS:
- Min. Order:
- 100g
- Purity:
- 98%+
- Supply Ability:
- 100kg
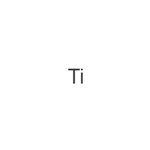
US $0.00/kg2022-09-27
- CAS:
- 7440-32-6
- Min. Order:
- 1kg
- Purity:
- 99%
- Supply Ability:
- 1000kg