Preparation of Phosphoric acid tris(2-chloro-1-methylethyl) ester
Phosphoric acid tris(2-chloro-1-methylethyl) ester is a flame retardant of low hydrolytic stability, used in polyurethane (PU) rigid and flexible foam, PVC, EVA and phenolics and epoxy resin.
Phosphoric acid tris(2-chloro-1-methylethyl) ester can be prepared according to the reported literatures[1-4].
Method 1
In a 5000 L stirred phosphorus oxychloride metering kettle equipped with a solid feeder, 4600 kg of phosphorus oxychloride was pumped first,Then add 15 kg of anhydrous aluminum trichloride catalyst through a solid feeder,Stirring at room temperature,Dissolved in phosphorus oxychloride solution,Propylene oxide continuously packed with a dehydrating agent calcium oxide dehydration tower and collected in a metering tank 10000L CCP 5300 kg,Detected by the water content of propylene oxide in the measuring tank is 28PPM,10000L simultaneously to the kettle and a solution of phosphorus oxychloride was added after the dehydration catalyst comprising propylene oxide, Feed process control reaction temperature at 65 ,Feed process control both the feed rate, Make it the weight ratio of phosphorus oxychloride:propylene oxide = 1: 1.152,Add the material in proportion at the same time continue to 65 insulation until the reaction is complete,The reaction will be good crude TCPP 16000L washing tank, Add 5000 kg of 1percent strength sodium hydroxide solution,At a temperature of 70 ° C,Stirred for 1 hour,Standing,Points to the base layer,Then add 5000 kg of deionized water,At a temperature of 70 ° C,Stirred for 1 hour,Standing,Points to the water layer,The washed TCPP crude into the dehydration kettle,Heating vacuum dehydration,The final product filter 9715 kg,The yield was 98.1percent;By GC analysis, TCPP ether content: 226PPM.
Method 2
The reactor charged with tris(chloropropyl) phosphate was fed continuously with propylene oxide (52.5 ml/h) and aluminium trichloride in solution in phosphorus oxychloride (21.6 ml/h). The reaction was carried out with a pump circulation rate of 1638 ml/h. The catalyst concentration was varied, as was the reaction temperature. After a run time of 6 h, samples of the tris(chloropropyl) phosphate discharged were taken, and the product composition was analysed by gas chromatography. Table 1 shows the conversion of the reaction, measured as residual propylene oxide (GCpercent), and the isomer composition, both as a function of the catalyst concentration and the reaction temperature.
Method 3
The reactor charged with tris(chloropropyl) phosphate was fed continuously with propylene oxide (52.5 ml/h) and the catalyst titanium tetrachloride or aluminium chloride, in solution in phosphorus oxychloride (21.6 ml/h). The reaction was carried out with a pump circulation rate of 1638 ml/h in reactor 1. The catalyst concentration was varied, as was the reaction temperature. After 6 h in each case a sample of 250 ml of tris(chloropropyl) phosphate was taken. Following removal of volatile constituents under reduced pressure on a rotary evaporator (80° C., 15 mbar, 0.5 h), the product composition was analysed by gas chromatography (GC) (Table 2).Subsequently the products were purified in a three-stage water scrub. This was done by combining the sample of 250 ml of 5-molar HCl in a vol/vol ratio of 1:1 at 90° C. Following phase separation, the organic phase was washed with water, 0.2 m aqueous sodium hydroxide solution, and again with water, in each case in a vol/vol ratio of 1:1 at 90° C. After phase separation, the products were dried on a rotary evaporator for 2 h at 80° C. and 15 mbar and were analysed by gas chromatography, and their physical parameters were ascertained as well.
Method 4
The reactor charged with tris(chloropropyl) phosphate was fed continuously with propylene oxide (52.5 ml/h) and aluminium trichloride in solution in phosphorus oxychloride (21.6 ml/h). The reaction was carried out with a pump circulation rate of 1638 ml/h. The catalyst concentration was varied, as was the reaction temperature. After a run time of 6 h, samples of the tris(chloropropyl) phosphate discharged were taken, and the product composition was analysed by gas chromatography.
References
1. Zhejiang Wansheng Co., Ltd. Shen G, Wang F, Jin Y. A three - (2 - chloroisopropyl) phosphate ester preparation method (by machine translation). CN105085568[P], 2017, B, Paragraph 0031-0038.
2. Weiss T, Elbert R. Preparation of phosphorus-containing propoxylation products by using aluminium trichloride. US2008/227997[P], 2008, A1, Page column 3.
You may like
Related articles And Qustion
See also
Lastest Price from Tris(1-Chloro-2-Propyl) Phosphate manufacturers
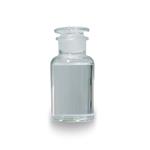
US $0.00-0.00/Kg2024-04-03
- CAS:
- 13674-84-5
- Min. Order:
- 1Kg
- Purity:
- 99.9%
- Supply Ability:
- 20 tons
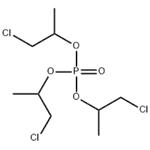
US $100.00-1.00/KG2024-03-25
- CAS:
- 13674-84-5
- Min. Order:
- 1KG
- Purity:
- 99%
- Supply Ability:
- g-kg-tons, free sample is available