Two synthesis processes of Isobutyl vinyl ether
Description
Isobutyl vinyl ether (IBVE), also known as vinyl isobutyl ether, 2-methyl-1- vinyloxypropane, 1-(vinyloxy)-2-methyl-propane, 1-(ethenyloxy)-2-methylpropane and isobutoxyethene, is a derivative of isobutanol and acetylene. IBVE is a colorless, transparent, and flammable liquid with an etheric aroma and low toxicity. Isobutyl vinyl ether is miscible with alcohols, ethers, esters, and aromatic hydrocarbons. It is slightly soluble in water.
Synthesis method
In industry, the acetylene route is mainly used to produce IBVE. IBVE is produced by vinylation of isobutanol with acetylene in the presence of a catalyst:
Commonly used catalysts for the acetylene process are alkali metal hydroxides (NaOH and KOH) and alkali metal alkoxides (sodium alkoxide and potassium alkoxide). The catalytic activity of KOH is greater than that of NaOH. The alkali metal elements of potassium and sodium can also be directly used as catalysts. However, the catalytic efficiency is low, and hydrogen gas is generated, which is disadvantageous to the reaction process so they are rarely used. Potassium isobutoxide obtained by reacting potassium hydroxide with isobutanol has high catalytic activity and is usually used in producing IBVE in industry. The processes for the manufacture of IBVE by the acetylene route include the gas-the-gas-liquid reaction process and the liquid-phase reaction process. The states of acetylene in the reactors of the two processes are quite different.
Gas-liquid reaction process
Common reactors for the production of IBVE by gas–liquid reaction process include autoclave, spray tower, bubble tower, and loop reactor. The autoclave is generally used for batch production, while the spray tower, bubble tower, and loop reactor are used for continuous production. Using dimethylaniline as a solvent and potassium isobutoxide as a catalyst, a stainless steel autoclave was applied for batch production of IBVE from acetylene and isobutanol. The reaction temperature was increased, and the vapor pressure of the alcohol was reduced in the solvent dimethylaniline with a high boiling point. The reaction was carried out at a temperature of 160 °C and under a pressure of 0.5 MPa for 7 h. The conversion of isobutanol was more than 70%. This method is simple and has no tail gas emission. However, a large amount of toxic dimethylaniline needs to be separated and recovered after the reaction, and the catalyst dosage is large (potassium isobutoxide is 10% of the mass of isobutanol), leading to a high production cost. In addition, the industrial scale-up of equipment is difficult.
Compared to the spray tower, the conversion per pass of isobutanol in the bubble tower was improved to more than 80%, and the overall yield of IBVE was 98%. The specific operation process is as follows: Isobutanol solution containing 12–20% potassium hydroxide was introduced into the bubble tower, and the liquid level in the tower was controlled to be 50–80%. After the moisture was removed by freeze-drying, acetylene gas was compressed and subjected to impurity removal by a drying tower. Then, the acetylene and isobutanol protective gas were uniformly mixed through a nozzle from the bottom of the tower and introduced into a bubble tower. The reaction occurred at 125–150 °C and 0.3–0.6 MPa. The reaction solution at the tower bottom was sent to a heat exchanger by a circulating pump to remove the heat released by the reaction and returned to the tower from the top for circulation. The formed small acetylene bubbles were fully in contact with isobutanol in the bubble tower for reaction. The generated IBVE, unreacted acetylene gas, and isobutyl alcohol were discharged from the top of the bubble tower, cooled, and then collected in a receiving tank. The unreacted acetylene gas was recycled. During the reaction process, the pump continuously replenished fresh raw material isobutanol and catalyst, and the deactivated catalyst was regularly discharged.
Full liquid–phase cyclic reaction process
Li’s research group at Xiamen University developed a process for continuous production of IBVE from acetylene and isobutanol by full liquid-phase cyclic reaction in a tubular reactor. Pure acetylene gas was dissolved in the isobutanol solution containing 3% potassium isobutoxide at low temperature and low pressure in advance. A solvent such as N-methyl pyrrolidone could be added to improve the solubility. Subsequently, the solution saturated with acetylene was pressurized by a plunger metering pump and introduced into a tubular reactor for a full liquid-phase reaction at a temperature of 155 °C and a pressure of 6–8 MPa. The residence time of the reaction solution in the reactor was 260 s. The outlet solution from the reactor was cooled and decompressed by a pressure relief valve, a small portion of the solution was discharged as the product, and the rest of the solution was circulated back to an absorber to absorb acetylene together with the feed liquid (isobutanol and catalyst). Then, the solution is pressurized and introduced into the tubular reactor for continuous reaction. At steady state, the conversion of isobutanol reached 77.5%, and the selectivity of IBVE was up to 97.3%.
You may like
Related articles And Qustion
See also
Lastest Price from Isobutyl vinyl ether manufacturers
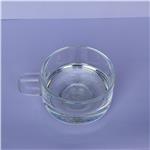
US $10.00/KG2025-04-21
- CAS:
- 109-53-5
- Min. Order:
- 1KG
- Purity:
- 99%
- Supply Ability:
- 10 mt

US $0.00-0.00/Kg2025-04-21
- CAS:
- 109-53-5
- Min. Order:
- 1Kg
- Purity:
- 99.99%
- Supply Ability:
- 20 tons