Process for preparing Tetrabenzylthiuramdisulfide
Description
The present invention relates to a method for preparing disulfide tetrabenzyl thiuram, particularly to a hydrogen peroxide and an acid in the presence of dibenzylamine, prepared sodium disulfide with carbon disulfide tetrabenzyl thiuram method below.
Background technique
Disulfide tetrabenzyl thiuram generally abbreviated as TBzTD, having the formula: TBzTD is an excellent rubber vulcanization accelerator. It is a high molecular weight, low volatility secondary amine based low molecular weight secondary amines not as easy nitrosamines. Thus, it processed better security than tetramethyl thiuram disulfide (TMTD) having a longer scorch time as TMTD can replace natural rubber, styrene-butadiene rubber and NBR fast curing primary accelerator or boosters, can effectively improve the cure rate and cure efficiency rubber, does not affect the processability and the dynamic properties of rubber vulcanizates without blooming, rubber having better thermal stability. Thus, tetrabenzylthiuram disulfide, thiuram vulcanization accelerators widely used in the rubber system.
Patent disclosure in Japanese Unexamined Patent Publication 63-238146 discloses a method of using a disulfide tetrabenzyl thiuram, in this patent will disulfide tetrabenzyl thiuram for rubber, vulcanized solved using other bring rubber accelerators surface blooming problems.
Chinese Patent Publication No. CN1341097A discloses a process for preparing a tetraalkyl thiuram disulfide in the presence of oxygen and a metal catalyst, Chinese Patent Publication No. CN1316422A discloses a method of using isopropanol, diethylamine and carbon disulfide was prepared disulfide, tetraethyl thiuram preparation. However, the presence of the significant drawback of the method, the process conditions in Chinese Patent Publication No. CN1341097A requires a certain pressure, and high equipment requirements; Patent Publication No. CN1316422A using isopropanol as solvent, the higher cost and not environmentally friendly, so Not prepared tetrabenzylthiuram disulfide thiuram used.
SUMMARY
The present invention is a technical problem to be solved is to disclose a disulfide tetrabenzyl thiuram preparation process, to overcome the above drawbacks of the prior art.
The method of the present invention comprises the steps of: carbon disulfide was added and the mixture was dibenzylamine aqueous sodium hydroxide solution, 30min-10h reaction at a temperature of 0 ~ 80 ℃, then adding an oxidizing agent and an aqueous solution of sulfuric acid, at a temperature of 0 ~ 70 ℃ 1 to 10 hours, the reaction product was collected from the four disulfide benzyl thiuram, yield 96%, purity 97% or more.
The reaction formula is as follows: He said oxidizing agent as a hypochlorite or hydrogen peroxide or a mixture thereof; in the preparation process of the present invention, the reaction temperature, dibenzylamine, the amount of sodium hydroxide and carbon disulfide, sodium hydroxide concentration will affect product formation , according to the preferred aspect of the present invention: as used dibenzylamine, molar content of sodium hydroxide and carbon disulfide were accounted for 30-35% of the total molar amount of the three materials, 30-35%, 30-40%; the amount of the oxidant 10% to 30% by mass of benzyl diamine; by weight aqueous sulfuric acid concentration is 5 to 50%;
The amount of the aqueous solution of sulfuric acid in terms of 100% sulfuric acid, 75 to 85% by mass of the oxidizing agent.
Seen from the above disclosed technical solution, the method of the present invention, simple operation, an aqueous solution of the reaction under atmospheric pressure conditions, no organic solvents, the high pressure required to overcome the past, organic solvent such as isopropanol is added and other shortcomings. Thus environmental pollution, no toxic to the operator, and a high product purity, easy industrialization embodiment.
Detailed ways
After Example 1 10.1g of sodium hydroxide and 300g of water was added into a reactor 49.3g dibenzylamine and stirred to dissolve, stir, carbon disulfide dropwise addition of 20g, the reaction temperature is controlled at 40 ℃, addition was complete, stirring was continued for 4h . 19g diluted concentration of 27.5% hydrogen peroxide water to 100g, 16g and a concentration of 98% sulfuric acid was diluted with water to 200g, and sulfuric acid and hydrogen peroxide solution was added dropwise, controlling the temperature at 65 ℃, after the addition was complete, the resulting a pale yellow precipitate was filtered and dried to obtain 65g disulfide tetrabenzyl thiuram. Yield 95%, purity 97%.
Example 2 After 10.1g of sodium hydroxide and 300g of water added to the reactor was added 49.3g dibenzylamine and stirred to dissolve, stir, carbon disulfide dropwise addition of 20g, the reaction temperature is controlled at 40 ℃, addition was complete, stirring was continued for 2h . The formulated 6g sodium hypochlorite solution concentration of 6%, and 98% dilute sulfuric acid with water to a concentration of 200g 16g, and simultaneously added dropwise a solution of sulfuric acid and sodium hypochlorite, controlling the temperature at 55 ℃, after the addition was complete, the resulting a pale yellow precipitate was filtered and dried to obtain 62g disulfide tetrabenzyl thiuram.
Yield 91%, purity 97%.
You may like
Lastest Price from Tetrabenzylthiuramdisulfide manufacturers
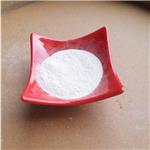
US $0.00-0.00/KG2025-04-15
- CAS:
- 10591-85-2
- Min. Order:
- 1KG
- Purity:
- 99%
- Supply Ability:
- 500000kg
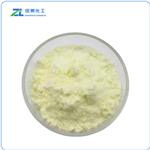
US $99.00-35.00/kg2025-04-15
- CAS:
- 10591-85-2
- Min. Order:
- 1kg
- Purity:
- 99%
- Supply Ability:
- 20ton