Description
Poly-p-xylylenes (PPXs), generally referred to their tradename as parylenes, a unique class of polymers, are obtained by cyclophane-based chemical vapor deposition (CVD) polymerization for diverse material applications. The chemical inertness, high purity, flexibility, mechanical strength, and stability of parylenes offer enormous potential in surface modification, optoelectronics, and drug delivery systems and have demonstrated technological utility for coatings of industrial products (e.g., clinically used biomaterials and biomedical devices)[1].
Chemical Properties
The most significant property of poly-p-xylylene is its thermal stability.
The crystalline melting point is 375-425°C and in an inert atmosphere the material is claimed to have a useful life of 10 years at 220°C. The thermal
stability in air is not exceptional. Poly-p-xylylene also maintains useful
properties at temperatures as low as - 200°C. The polymer has outstandingly
good electrical insulation characteristics and is used as a dielectric in special
capacitors.
It may be noted that poly-p-xylylene is considerably less stable than polyp-
phenylene owing to the presence of the relatively weak dibenzyllinkages. It
may also be noted that the isomeric polyxylylenes have been prepared but
poly-o-xylylene has a polymer melt temperature of 110°C whilst poly-mxylylene
has a softening temperature of only 60°C; these polymers are
therefore of no immediate interest.
Uses
Poly-p-xylylene (PPX) is mainly used as protective coatings, e.g. in electronics, medical devices and paper products, or as sealing materials to prevent additives from leaking out of elastomers. PPX can also be used in micro-electro-mechanical systems, organic light-emitting diodes, or in biological and medical applications. A relatively new area of PPX research is the formation of reactive coatings. This can be achieved through the introduction of functional groups capable of reacting in a polymer-like reaction.
Preparation
When di-p-xylylene is pyrolysed, both methylene bridges are homolytically
cleaved to give the reactive intermediate p-xylylene which spontaneously
forms the linear polymer on cooling. Generally, the polymer is deposited (in
the polymerization chamber) on to a cold condenser and then removed as
film; alternatively, the polymer is deposited directly on to an object which is
required to be coated. Typically, an average molecular weight of about
500000 is attained.
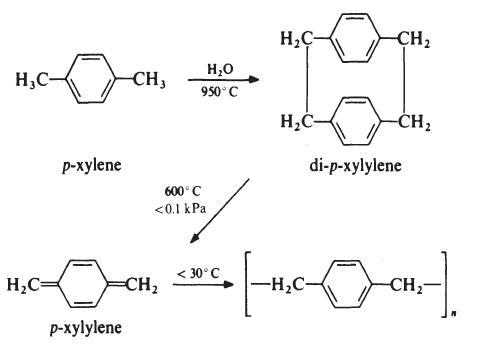
References
[1] Salma Begum and Manuel Tsotsalas*. “Solid and Hollow Poly(p-xylylene) Particles Synthesis via Metal–Organic Framework-Templated Chemical Vapor Polymerization.” Chemistry of Materials (2022).