Chemical Properties
Poly(m-phenylene isophthalamide) has an extremely high melting point
(380-390°C) and cannot be melt processed by the usual means. Commercial
material is supplied as fibre and as a paper and is used directly in these forms.
Fibre is prepared by extruding a solution of the polymer in a mixture of
dimethylformamide and lithium chloride into hot air. The aromatic polyamide
papers are produced from a combinati~n of chopped fibres and
chopped film (prepared continuously by interfacial polymerization).
At ordinary temperatures, poly(m-phenylene isophthalamide) has mechanical
properties comparable to those of the aliphatic nylons but at elevated
temperatures the aromatic polymer is greatly superior. Broadly, the mechanical
properties of poly(m-phenylene isophthalamide) show little change up to
about 200°C. The aromatic polymer also shows little change in electrical
insulation properties over a similar temperature range. The polymer resists
ignition and is free of after-glow. The chemical resistance of poly(m-phenylene
isophthalamide) appears to be generally similar to that of the aliphatic nylons
except that resistance to mineral acids is rather better. The fibre is used for
heat and flame protective clothing. The paper has found use in electrical
insulating applications where resistance to elevated temperatures is required.
Uses
Poly[N,N′-(1,3-phenylene)isophthalamide] is used in heat and flame protective clothing. Electrical insulating paper requiring high temperature stability.
Preparation
Poly(m-phenylene isophthalamide is produced by reaction of isophthaloyl
chloride and m-phenylenediamine:
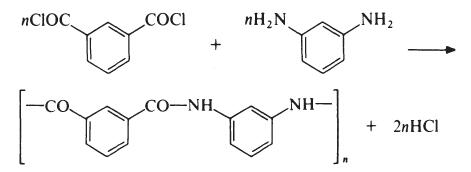
This reaction occurs rapidly in the presence of an acid acceptor under mild
conditions. The conventional melt polymerization techniques, as used for the
preparation of nylons, cannot be applied to aromatic polyamides since the
melting points of the polymers are too high. Polymerization is therefore
conducted either in solution (e.g. in methylene chloride) or in suspension. In
the latter case, the diamine is dissolved in water, together with an acid
acceptor (e.g. sodium carbonate) and the diacid chloride is dissolved in a
solvent which is immiscible with water (e.g. carbon tetrachloride or cyclohexanone).
The two solutions are then subjected to intensive mixing. Rapid
reaction occurs at the liquid interface or just inside the solvent boundary and
this technique is therefore commonly termed interfacial polymerization.