Copper Pyrithione
Bacground
Pyrithiones (2-mercaptopyridine-N-oxide, salts thereof, and bis-2,2' derivatives) are known to be excellent biocides in paint formulations. Combinations of zinc pyrithione and cuprous oxide are known to be excellent antifouling agents when formulated into paints and paint bases (i.e., the paint before pigment addition) also containing resin, as disclosed, for example, in U.S. Pat. No. 5,057,153. Unfortunately, however, such paints may have a limited service life due to leaching of the biocide from the paint film during use.
Copper pyrithione is known to have lower solubility in water than zinc pyrithione. Such low solubility would provide an extended period of antimicrobial activity for copper pyrithione relative to zinc pyrithione during use. Unfortunately, copper pyrithione is not commercially available, possibly due to the fact that its manufacture is surprisingly more difficult than the readily available zinc pyrithione, sodium pyrithione and bis-2,2'-pyrithione and its adduct with magnesium sulfate. The present invention overcomes this problem of lack of commercial availability of copper pyrithione by providing for the generation of copper pyrithione in-situ in the paint formulation through the reaction of another pyrithione compound with cuprous oxide in the presence of a controlled amount of water. Such a solution would be highly desired by the paint manufacturing community.
In Situ Generation of Copper Pyrithione in a Paint
A stock solvent mixture was prepared by mixing xylene and methylisobutyl ketone in a 60:40 weight ratio and then adding sufficient water to water to provide a mixture containing about 0.2% water. The mixture was analyzed for water by Karl Fisher titration and found to contain 0.17% water. A paint was made from the following ingredients (amounts shown are in grams):
______________________________________
Ingredient Amount
______________________________________
Zinc Pyrithione 12.0
VAGH Resin 5.8
Cuprous Oxide 140.0
Wood Rosin WW 12.0
Stock Solvent 70.0
______________________________________
A one pint can was charged with the VAGH resin (a terpolymer of vinyl alcohol, vinyl acetate, and vinyl chloride manufactured by the Union Carbide Corporation) dissolved in 20.5 grams of the stock solvent. Next were added the cuprous oxide and the zinc pyrithione gradually using an additional 12.0 grams of solvent to aid mixing. These materials were ground in a high speed disperser at 7000 rpm for one hour. A water bath was used to keep the temperature of the mixture at a maximum of 45° C. Then the wood rosin was predissolved in the balance of the solvent mixture and added to the formulation. Mixing was continued for an additional hour at 4000 rpm. The formulation was cooled to room temperature and weighed. Solvent lost to evaporation was replaced. Based on the water content of the solvent used, this formulation contained 0.05% water. After standing for one day, formation of green solids characteristic of copper pyrithione was observed in the formulation. Analysis by infrared adsorption spectroscopy (attenuated total reflectance) showed no band at 821.5 cm-1, which is characteristic of zinc pyrithione, but a strong band at 831.2 cm-1, which is characteristic of copper pyrithione.
You may like
Related articles And Qustion
Lastest Price from Copper Pyrithione manufacturers

US $30.00-10.00/KG2025-04-15
- CAS:
- 14915-37-8
- Min. Order:
- 50KG
- Purity:
- 99%
- Supply Ability:
- 500000kg
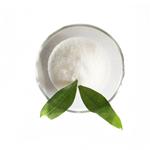
US $0.00/KG2025-03-21
- CAS:
- 14915-37-8
- Min. Order:
- 1KG
- Purity:
- 99%
- Supply Ability:
- 50000KG/month