Product Description
Name | 1,10-Diaminodecane | EINECS | 211-471-9 |
CAS No. | 646-25-3 | Density | 0.857 g/cm3 |
PSA | 52.04000 | LogP | 3.42520 |
Solubility | 5.9g/L at 20℃ | Melting Point | 62 °C
|
Formula | C10H24 N2 | Boiling Point | 140 °C12 mm Hg(lit.) |
Molecular Weight | 172.314 | Flash Point | 127.1°C |
Transport Information | UN 3259 8 | Appearance | white to light yellow powder and chunks |
Appearance and properties: white to light yellow powder and blocks
Boiling point: 140 °C12 mm Hg(lit.)
Melting point: 62 °C
Production method
It is obtained by catalytic hydrogenation reduction of sebaconitrile. 1, 10-sebaconitrile and the Raney nickel catalyst suspended in 95% ethanol were loaded into a high-pressure reactor with a capacity of 1.1L, and liquid ammonia was fed, followed by hydrogen gas to a pressure of 10.34MPa, and the temperature was raised to 125 ° C until the hydrogen was no longer absorbed, and the hydrogen and ammonia were cooled to escape. Ethanol was injected into the reactor to wash out the reaction products, and then the ethanol solution was decolorized and filtered, the catalyst was removed, and the ethanol was often pressurized and evaporated, and the decompressive distillation was carried out, and the 1, 10-decamethylene diamine product was obtained by collecting the fraction of 143-146℃ (1.867kPa). In addition,1, 10-decamethylene diamine can also be prepared from decamethylene glycol with Raney nickel as catalyst at 220-260℃.
2. Alloy melting and crushing according to the ratio (alloy ratio: electrolytic nickel 38% ~ 45%, electrolytic aluminum 50% ~ 57%, chromium 1% ~ 3%, iron 3% ~ 5%) the accurate metal nickel and aluminum are installed in two or combined in a crucible, placed on the open coke furnace with a blower to heat. When the aluminum is peach red and the nickel is yellow red, the iron and chromium that have been preheated to red are immediately put into the crucible quickly, and the graphite rod is stirred for 10 to 15min. The fan is stopped, the molten alloy is poured into the cast iron tray, and immediately quenched with cold water to obtain the gray brittle nickel-aluminum alloy. The alloy can also be melted by high frequency inductance furnace, but the activity of the skeleton nickel catalyst is affected to some extent. The alloy is crushed and screened, and the particle size is 60 ~ 120 mesh as alloy products.
3. Alloy dissolution according to the ratio (mass) of alloy powder: solid alkali: water = 1∶1∶ (3 ~ 4), the alkali is first prepared into 25% aqueous solution, and the aluminum is dissolved in the reactor with stirring and heat transfer jacket and coil. Control the temperature of 50 ~ 60℃, add all the lye within 4 ~ 6h, then heat up to 100 ~ 110℃, maintain 6 ~ 8h after unloading, and then wash with 60 ~ 80℃ distilled water to neutral, that is, get activated skeleton nickel catalyst. The activation process is as follows: the sodium metaaluminate produced by aluminum and sodium hydroxide in the reaction process is washed away. The aluminum of the reaction accounts for more than 60% of the total aluminum, and the remaining aluminum forms a skeleton to support the nickel, so it is called skeleton nickel. After activation, the catalyst particles are honeycomb, with large specific surface and porosity, in which a large number of hydrogen atoms are adsorbed [H]. Because [H] is prone to spontaneous combustion in the air, it is generally called "active hydrogen". The higher the content of active hydrogen in the activated matrix nickel catalyst, the easier it is to spontaneous combustion, indicating that the activity is also stronger. The activated skeleton catalyst must be stored in ethanol or non-ionized water.
Use
Organic synthetic raw materials, used for polymer polymerization and drug refining, and used as reagents. Used as epoxy resin curing agent, dosage 25 parts, curing conditions 25℃/7 days or 60℃/5h. This product is an intermediate of nylon 1010 and is also used as a raw material for organic synthesis.
Company Profile
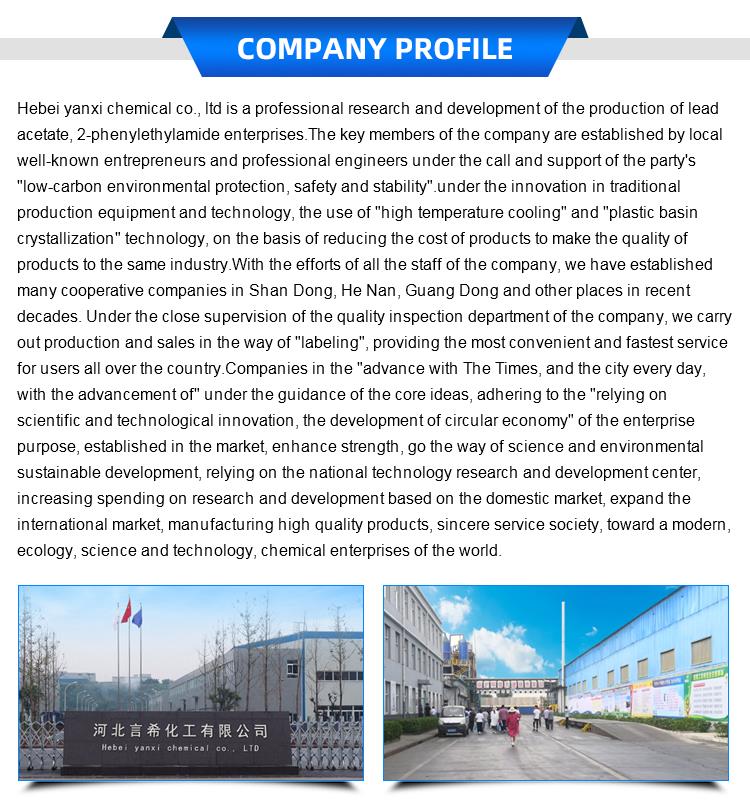
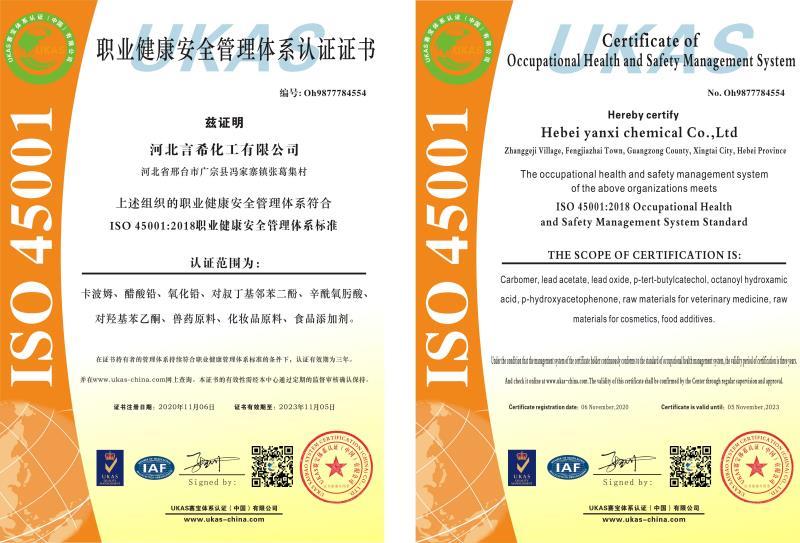
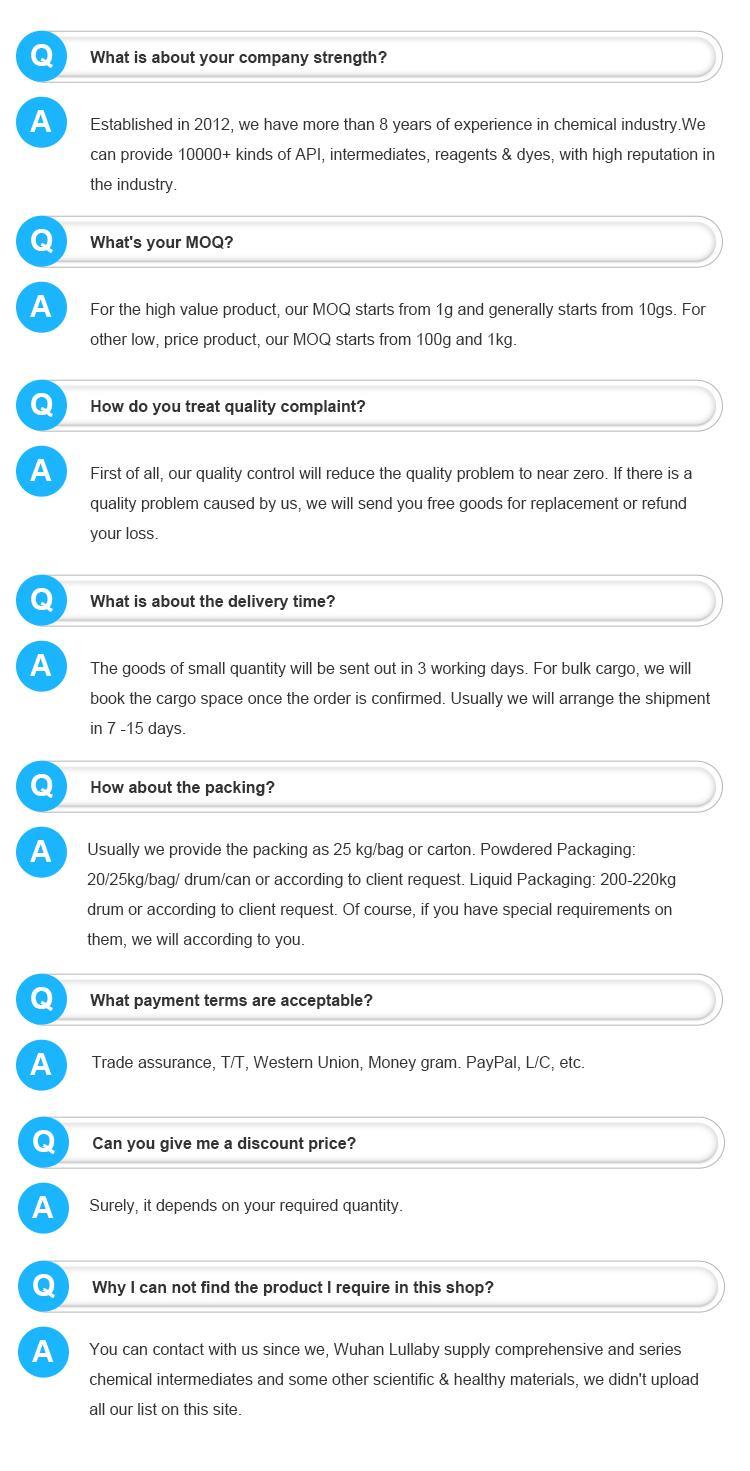